Mech-Viz 1.7 Release Notes
This document introduces the new features, improvements, and resolved issues of Mech-Viz 1.7.
Mech-Viz 1.7.5 Release Notes
This topic introduces the resolved issues inMech-Viz 1.7.5.
Resolved Issues
The following issues have been resolved in Mech-Viz 1.7.5:
-
When the Update Info Source of the “Update Held Workobject” Step was set to Property Value, the workobject label was lost after the workobject was updated.
-
When the “Vision Continue Palletizing” Step was used to continue palletizing and a full stack was formed, an extra alert would pop up.
-
Loading an abnormal STL model caused the software to crash.
-
When the Keep Last Exec State option was enabled in the toolbar and Update Bin Pose with Vision was selected in the “Vision Move” Step, the collision detection for the bin would be invalid.
-
When Update Bin Poses with Vision was selected in the “Vision Move” Step, the logic sequence for determining whether the pick point is inside the bin and updating the bin pose was incorrect.
-
The original_vision_result field was missing from the data sent by Mech-Viz, resulting in an error in the data sent by Command 110 in Standard Interface communication.
-
When multiple “Vision Move” Steps shared the vision result, only the first “Vision Move” Step could output the original_vision_result field. Although subsequent “Vision Move” Steps could plan successfully, this field was empty, resulting in an error in Standard Interface Command 110. After the issue is fixed, all “Vision Move” Steps can output the original_vision_result field.
-
When Sharing Vision Result and Filter Vision Result were enabled in multiple “Vision Move” Steps, the previous “Vision Move” Step mistakenly deleted the pick points corresponding to its unwanted labels, resulting in a planning failure of the second “Vision Move” Step. After the issue is fixed, the pick point corresponding to the unwanted label of the first “Vision Move” Step will be retained for the planning of the second “Vision Move” Step.
-
In the workflow prior to the “Vision Move” Step, if the “Classify” Step was present in some branches but not in others, the software would report an error when executing the branch without the “Classify” Step.
-
If the Classify before “Vision Move” option was selected in the “Classify” Step, and the Select Step Name was set to a “Vision Move” Step, and then the Classify before “Vision Move” option was unselected, the Classify before “Vision Move” option would be automatically re-selected after the Step was executed.
-
Removed the redundant Get, Set and Show buttons in the Relative rotation in tool frame section of the “Relative Move” Step.
-
The old parameters that were indicated for deletion in the collision detection configuration window due to compatibility issues were not deleted from the actual project files.
Mech-Viz 1.7.4 Release Notes
This topic introduces the resolved issue in Mech-Viz 1.7.4.
Improvements
Added Region-Specific Software License Control
The software license is updated to add the restriction of using the software in regions where the software is purchased.
In Mech-Viz 1.7.4, you can go to
to check the software license and region restrictions.Removed “System Language” from the Software “Language” Option
From Mech-Viz 1.7.4, “System Language” has been removed from the “Language” option (
) of the software. If the operating system language of the computer is not a language supported by the software (English, Simplified Chinese, Japanese, or Korean), the default language when the software is installed for the first time is English.This improvement has resolved the following two issues:
-
The link redirection failed and Step names were displayed abnormally in the software when the operating system language of the computer was not a language supported by the software.
-
The language pack could not be loaded successfully according to the operating system language of the computer.
Resolved Issues
Mech-Viz 1.7.4 has fixed the following issues:
-
The “Delete Object” option in the context menu of the simulation area was not been disabled during project simulation or running.
-
When the workobject rotational symmetry and tool rotational symmetry settings are applied at the same time, an error might occur in the workobject rotational symmetry attempt.
-
When there was not a move-type Step before the “Branch by Msg” Step, the Out Port When Skip setting would not take effect.
-
The vision result labels were lost after reusing vision results.
-
Drag any log entry might cause the software to crash.
-
After enabling “Limit Total Count” in the “Vision Move” Step, not all possible grouping results were provided.
-
The suction cup DO that was planned by using the “Vision Move” Step might be incorrect.
-
When the “Vision Continue Palletizing” Step was used to match the pallet pattern, the orientation of the pallet might be incorrect.
-
When the workobject model is a custom model, an collision might be missed during the collision detection.
Mech-Viz 1.7.2 Release Notes
This document introduces the new features, improvements, and resolved issues of Mech-Viz 1.7.2.
Improvements
Simulating All Planned Waypoints
In previous versions, if “Send Waypoint” was not selected for a move-type Step, the corresponding waypoint would only be involved in the path planning, and the simulated robot would not move to this waypoint.
In Mech-Viz 1.7.2, the simulated robot will move along all planned waypoints by default.
If you want to keep the previous setting, please adjust it in Settings > Options > Basic settings.
STL and DAE Source Files Will Be Retained after Robot Exporting
In previous versions, the STL and DAE source files of the robot would be deleted while the robot was exported.
In Mech-Viz 1.7.2, the STL and DAE source files of the robot will be retained after the robot is exported.
Removed the “Side Vacuum Gripper” Option
In previous versions, the “Side vacuum gripper” option can be configured in the “Vision Move” Step and “Tools”. This feature was used for depalletizing applications in which the side vacuum gripper was used as the end tool.
From Mech-Viz 1.7.0, the “Depalletizing vacuum gripper” option covers all features of the “Side vacuum gripper”.
Therefore, the “Side vacuum gripper” option is removed in Mech-Viz 1.7.2. Please re-configure the “Depalletizing vacuum gripper” option if you used the “Side vacuum gripper” option previously.
Supported More Euler Angle conventions
In previous versions, only 5 common types of Euler angles were supported. In Mech-Viz 1.7.2, another 13 types of Euler angles are supported as well.
Resolved Issues
Mech-Viz 1.7.2 has fixed the following issues:
-
The transparency status of “Tools” set in the “Resources” panel was not consistent with that of the tool in the simulation area.
-
The “Set effective range for pose” feature for bins in “Scene objects” did not take effect.
-
The software might crash when the “Smart Obstacle Avoidance” feature was used.
-
When the “All Waypoints in One Move” feature was used in the “Move by List” Step, certain waypoints might be missed.
-
When the box dimensions were adjusted in the “Predefined Pallet Pattern” Step, the palletizing sequence would not be adjusted automatically according to the change of the pallet pattern.
-
When the “Mixed Pallet Pattern” Step was used, the box might be palletized on a position that had been occupied by a box.
-
The source Step of the pallet pattern had been selected in “Vision Continue Palletizing”, but a hint saying that no Step was selected popped up.
-
The box depalletizing algorithm considered the gap between suction cups as valid suction cup areas.
-
The output vision result of the box group did not contain labels for each box.
Mech-Viz 1.7.1 Release Notes
This document introduces the improvements and resolved issues of Mech-Viz 1.7.1.
Improvements
Modified the Default “Obstruction Tolerance Distance” in the “Vision Move” Step to 40 mm
In previous versions, the default value of “Obstruction Tolerance Distance” in the “Vision Move” Step was 20 mm, which was too strict for some on-site applications and thus caused Mech-Viz to discard many feasible picking solutions during the planning.
In Mech-Viz 1.7.1, the default value of “Obstruction Tolerance Distance” in the “Vision Move” Step has been modified to 40 mm.
Resolved Issues
The following issues are resolved in Mech-Viz 1.7.1:
Resources - Robot
-
Modifying the soft limits of the robot might cause a crash of the software.
-
There was an error in the visualization model of the FANUC R-2000iC/270F robot.
-
When the project was simulating or running, the “TCP” and “Joint positions” could not be switched in the Robot panel.
Resources - Tools
-
The toolbar could still be used when the Tool Configuration window was opened.
-
In the TCP Calibration window of the Tool Configuration window, the Input Flange Pose of Robot window could not be displayed properly after “Add pose” was clicked.
-
The unconfirmed change of the tool type would be saved when the Tool Configuration window exited.
Resources - Workobjects
-
The X-axis rotational symmetry and the Y-axis rotational symmetry could be set at the same time.
-
The toolbar could still be used when the Workobject Configuration window was opened.
-
The default workpiece configuration might be deleted.
Resources - Scene Objects
-
Configuring the scene object might cause a crash of the software.
-
The toolbar could still be used when the Scene Object Configuration window was opened.
-
When the bin was not involved in the collision detection, the vision pose would be considered outside the bin.
Step
-
If two “Relative Move” Steps were dependent on each other, the software would enter a dead loop.
-
The “Vision Continue Palletizing” Step might cause a crash.
-
After the “Multi Pick Palletizing” Step was reset, the palletized cartons remained unpalletized.
-
When the robot was not moving, the “Update Held Workobject” Step could not display the model of the held workobject.
-
The “Update Held Workobject” Step might cause a stuck on the software.
-
When the “Classify” Step was in front of the “Vision Move” Step, and the Avoid Picking on Save Workpiece feature was enabled in “Vision Move”, the software might enter a dead loop.
-
When another move-type Step was connected with the Other failures exit port of “Vision Move”, an error message still popped up.
Picking/Placing Planning
-
The “Only Group Complete Row” setting along Y-axis in the multi-pick depalletizing algorithm was not effective.
-
The “Only Group Complete Row” setting along Y-axis in the multi-pick depalletizing algorithm was not effective.
-
The “Multi Pick Depalletizing” might not match the pallet pattern successfully due to the floating-point error.
-
The picking solution in which more cartons are picked at once was not given priority in “Multi Pick Depalletizing”.
Built-in Tools
-
Using the “Pallet Editor” might cause a crash of the software.
-
The configuration in the “Tool Array Configuration” window could not be saved.
-
The vision records in the Set Vision Records window could not be loaded properly.
-
The modification of an existing pallet pattern by using the “Pallet Editor” could not be saved.
Mech-Viz 1.7.0 Release Notes
This document introduces the new features, improvements, and resolved issues of Mech-Viz 1.7.0.
New Features
New “Welcome” Interface
After the software is started or a project is closed, a “welcome” interface will be displayed. You can create a new project or open a recent project in the “welcome” interface.
New “Resources” Panel
In Mech-Viz 1.7.0, the original “Scene” and “Tools and Workobjects” functional panels are removed. The resources used in the project are re-organized and aggregated in Resources, which is a new tool to manage the project resources.
The aggregated “Resources” include project, robot, reference frames, tools, floor, scene objects, and model library.
-
Project: Display the project name, project modification status, and the project autoload status.
-
Robot: Display the robot model used in the current project.
-
Reference frames: Aggregate all reference frames in the 3D simulation area.
-
Tools: For creating and deleting tools and managing the existing tools.
-
Workobjects: For creating and deleting the workpiece configurations and managing the existing workpieces.
-
Floor: For adjusting the height of the floor.
-
Scene objects: For creating and deleting scene objects and managing the existing scene objects.
-
Model library: For managing all models used in the project. All models should be imported to the Model Library first and then utilized with other functions.
Added “Set as Active Tool”
The concept “active tool” has been introduced. The tool set as the “active tool” will be used for path planning when the new round of simulation/execution starts.
-
When the project is not simulating or running, right-click the name of the tool in the Resources panel and select “Set as Active Tool” to change the “active tool”.
-
When the project is simulating or running, you can change the “active tool” by using the “Change Tool” Step.
Added Automatic Layout Feature in the “Predefined Pallet Pattern” Step
The “Predefined Pallet Pattern” Step calculates based on the pallet size, dimensions of the carton, gap width, and limitation of the pallet height to generate a pallet pattern with the most cartons and layers, of which the layout of the odd layer and even layer is also appropriate.
Other Features
-
Added “New Project” option in the File menu.
-
Added robot models for ROKAE SR3 and ROKAE SR4 robots, and generated the corresponding special robot configurations.
-
You can select multiple Steps and use the shortcut Ctrl + G to pack them as a Procedure, and you can also use the shortcut Ctrl + Shift + G to unpack the selected Procedure.
-
Added a “Wait Timeout” port to the “Branch by Msg” Step. You can set a timeout period and the Step will take the “Wait Timeout” port to proceed if a timeout occurs.
-
You can save and import the pallet pattern in the offline mode of the “Mixed Pallet Pattern” Step.
-
Added a new feature to specify the direction of the palletized carton in the “Mixed Pallet Pattern” Step.
-
Added a new “Pinwheel 2” pallet type in the “Predefined Pallet Pattern” Step.
-
Added a new feature to adjust the workpiece orientation in the “Predefined Pallet Pattern” Step.
Improvements
Expanded the Robot Model Library
The number of robot models in the online robot model library has increased from 214 to over 600. Most robots from ABB, Denso, FANUC, Kawasaki, KUKA, MITSUBISHI, NACHI, UR, Stäubli, and YASKAWA have been included.
he parameters of robots from ABB, FANUC, Kawasaki, KUKA, NACHI, UR, and YASKAWA have also been calibrated during the model-making process, and therefore the robot parameters are more accurate.
Tool Collision Model in STL format is No Longer Supported
To achieve better performance of the collision detection between the tool and the point cloud, collision models of the tool in STL format are not supported anymore in Mech-Viz 1.7.0. Please refer to Note of the Models for model formats supported in the software.
Improved the Depalletizing Algorithm in the “Vision Move” Step
In Mech-Viz 1.7.0, the depalletizing algorithm in the “Vision Move” Step has been restructured and improved, and the following picking methods are supported.
Single-section vacuum gripper |
|
Multi-section vacuum gripper |
|
Pick a single object |
|
Pick multiple objects in a row |
|
Pick objects in multiple rows |
|
Center of the vacuum gripper coincides with that of the carton |
|
Midpoint of the vacuum gripper’s edge coincides with that of the carton’s edge |
|
Corner of the vacuum gripper coincides with that of the carton |
|
Long edges of objects are parallel to that of the vacuum gripper |
|
Long edges of objects are perpendicular to that of the vacuum gripper |
In addition, the software no longer restricts the X-axis of the TCP reference frame to be parallel to the long side of the vacuum gripper and the X-axis of the workpiece pick point reference frame to be parallel to the long side of the carton. There is no coupling between all the above features, and a variety of picking strategies can be configured by modifying the parameters.
Improved the Model Editor
-
A new “Set Frame” feature is added to the Model Editor. With this feature, you can set the origin and the directions of the axes for the reference frame. Therefore, the exported OBJ model can be accurately and quickly installed at the end of the robot flange.
-
The project in Model Editor is saved as M3D file and you do not need to create a folder to save the project.
-
OBJ models exported by Model Editor are compatible with Mech-Viz 1.6.0 and earlier.
Improved the Display Format of Euler Angles
The Euler angles are denoted differently on the teach pendant of different robot brands. For example, ABB uses EX, EY, and EZ; KUKA uses A, B, and C; while Kawasaki uses O, A, and T.
In Mech-Viz 1.7.0, the display formats of Euler angles for some robot brands are integrated in the software. Once a robot is selected, the software will automatically switch the display format of Euler angles to the one corresponding to the selected robot, and the characters used by the robot brand will be displayed in the interface.
Improved Tool Configurations
In Mech-Viz 1.7.0, the tool configuration window is re-organized and improved. The new tool configuration window consists of the tool type options and “Configure control logic” button, and the symmetry configuration parameters have been improved.
Improved Workobject Configurations
The new workobject configuration window in Mech-Viz 1.7.0 aggregated functions related to workobject configurations that were in different locations in the software. The new workobject configuration window provides settings of the rotational symmetry, picking relaxation, and solution selection strategy.
Improved Scene Object Configurations
In Mech-Viz 1.7.0, the interfaces used for creating new scene objects and configuring scene objects are combined, and parameters for setting the effective range for poses have been improved.
Renamed Steps
Starting from Mech-Viz 1.7.0, “Skill” and “Task List” have been renamed to “Step” and “Procedure”. In addition, the names of the following Steps have been updated in Mech-Viz 1.7.0 for easier understanding of the functions. In addition, the format of all Step names have been changed to title-style capitalization.
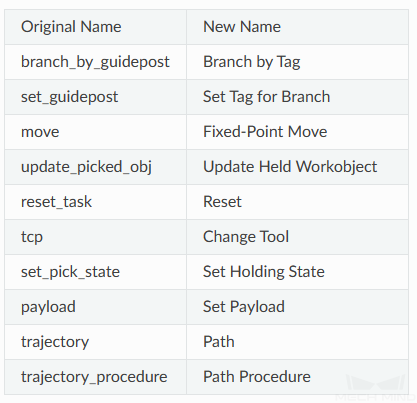
Other Features
Menu Bar
-
Removed the “Not Print Message Sent to Robot” option, and the messages sent to the robot will always be printed.
-
Removed the “Write Debug File (.dmp)” option. This feature is no longer supported.
-
Changed the default options of the global unit settings in Settings - Options from Use built-in units of Steps to mm and °.
Resources
-
Removed the “Autoload” button on the toolbar. You can go to the Resources panel, right-click the project name and select “Autoload Project”.
-
The interfaces used for suction cup configurations and tool configurations are combined, and the individual suction cup configuration file will not be saved.
-
When the tool configuration, workobject configuration, and scene objects configuration windows are opened, you can adjust the perspective and zoom in or out in the 3D simulation area at the same time.
Step
-
Re-structured the layout of the buttons used for fast setting, pose transformation, pose calibration, and pose editing in move-type Steps.
-
The maximum port number in the “Set DO List” is increased to 30000.
-
The “unfinished” port of the “Check Look” Step is renamed to “Timeout”.
-
Improved the log when multi-pick depalletizing is used in the “Vision Move” Step. The carton combination information and carton offset planning details are included.
-
A new “Failure” exit port is added to the “Update Scene Objects” Step when vision service is used as the source for updating.
-
When the “Vision Move” Step is used to pick multiple cartons at one time, the model of the cartons to be picked together are displayed as multiple individual cartons instead of a single large carton.
-
Removed the “Selected” option from the Relative Move Dependency option in the “Relative Move” Step.
-
Removed the “set_robotiq” and “call_robot_function” Steps.
-
Removed the Save Successful Vision Result parameter and related features in the “Vision Move” Step.
Robot Functional Panel
-
Added value display for the dynamic limits of joint positions that changes as another joint position is adjusted.
-
For YASKAWA PL80, MPL80II, and MPL100II that have different display formats of the joint positions, the display format of joint positions in the interface is updated to match the joint positions displayed on the robot end.
-
The tool list will not be cleared after the robot is switched.
-
If the robot used in the project is lost, you can re-select other robot models in the robot library.
Collision Detection
-
Whether the collision detection between the point cloud and others is enabled or not, the point cloud of the held workobject will be removed by the “Vision Move” Step.
-
Whether the collision detection between the point cloud and others is enabled or not, the point cloud will be reset after resetting the “Vision Look” Step.
Software Communication
-
Added the “Skip waypoints approximate to others” parameter, which can be used to determine whether to send two waypoints that are close to each other.
-
Removed the “Send Tcp Pose” option in the Others functional panel, and the software will always send the TCP.
Resolved Issues
Mech-Viz 1.7.0 has fixed the following issues:
-
When an project built with earlier version software had not been opened successfully, part of the workflow was still loaded.
-
When a project was locked, a new user could be registered without the password.
-
Occasionally, users would not be prompted to save changes when closing the project.
-
When the project was simulating or running, the scene objects could be moved by dragging the axis of their reference frames.
-
When the project was simulating or running, the scene objects could be moved by dragging the axis of their reference frames.
-
The installation of the robot model might fail if there were uppercase letters in the name of the robot installation package.
-
When a new tool was created, the TCP reference frame in the 3D simulation area would not change with the new configuration.
-
When the workflow display was formatted, some Steps might overlap.
-
The search object might change after the search feature in the Workflow panel was enabled/disabled.
-
The error message in the “Vision Move” Step was incorrect when the vision service was not triggered by the “Vision Look” Step.
-
The error message was inaccurate when the “Vision Move” Step reused the vision result and failed to plan a path.
-
The error message was incorrect when the count of held workobjects reached the set value in the “Vision Move” Step.
-
In the “Update Held Workobject” Step, although the “Update Info Source” had been set to “Vision Service”, the object dimensions might still be updated from the parameters.
-
When the model type of the workobject was a custom model, the workobject model could not move with the real workobject.