Depalletizing Vacuum Gripper (Single Pick)
The following parameters can be adjusted when the vacuum gripper is used for single-pick depalletizing.
Suction Cup Offset/Offset Strategy
When the vacuum gripper is used for box depalletizing, the vacuum gripper is fixed and cannot be changed in most cases. However, the vacuum gripper should be used to pick boxes of varied dimensions. To avoid picking non-target boxes in depalletizing, the robot may not pick the target box with the center of the vacuum gripper. Instead, the corner or other parts of the vacuum gripper will be used.
There are three offset strategies, i.e., Default Strategy, Custom Strategy Priority, and By Edge/Corner ID Sequence.
Default Strategy
When this strategy is adopted, the corners of the vacuum gripper will be prioritized for picking boxes.
Custom Strategy Priority
When this strategy is adopted, you can assign priorities to three strategies.
Strategy Priority
There are three available strategies, i.e., CenterToCenter, EdgeMidpointToEdgeMidpoint, and CornerToVertex. Please assign priorities to these strategies according to the actual requirement.
In the figure below, the orange rectangle represents the box, and the gray rectangle represents the vacuum gripper. The green part of the vacuum gripper indicates that the section is activated, while the red part indicates that the section is deactivated.
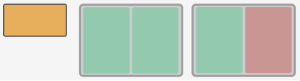
-
When a single section is activated
The figures below demonstrate the effects of using CenterToCenter, EdgeMidpointToEdgeMidpoint, and CornerToVertex from left to right.
-
When both sections are activated
The figures below demonstrate the effects of using CenterToCenter, EdgeMidpointToEdgeMidpoint, and CornerToVertex from left to right.
-
The effect is similar when there are more than two activated sections of the vacuum gripper.
Box Surface Coverage Lower Limit
This parameter specifies the minimum proportion of a box’s upper surface covered by the vacuum gripper when the vacuum gripper attempts to pick a box. If the coverage is larger than the value, it is considered that the vacuum gripper is able to pick the box.
Suction Cup Orientation
This parameter specifies the orientation of the vacuum gripper relative to the box group during picking.
You can set the Suction Cup Long Edge Orientation and Orientation Reference, and there are four relative positional relationships in total:
-
Long edges of objects are parallel to that of the vacuum gripper.
-
Long edges of objects are perpendicular to that of the vacuum gripper.
-
The long edge of the vacuum gripper is parallel to the direction along which the boxes are grouped.
-
The long edge of the vacuum gripper is perpendicular to the direction along which the boxes are grouped.
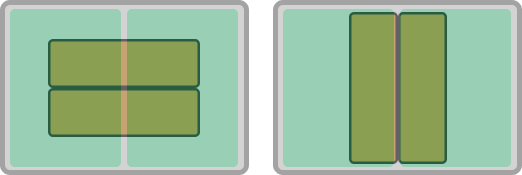
The figure on the left shows the effect when the long edge of the vacuum gripper is parallel to the long edge of the box group, and the figure on the right shows the effect when the long edge of the vacuum gripper is perpendicular to the long edge of the box group.
Offset Priority
You need to set a reference point to enable this feature. The offset strategies will be sorted according to the distance between the TCP and the reference point, and the offset strategy with a TCP closer to the reference point has a higher priority. Once Sort by Distance to Reference Point is selected, the following parameters will appear.
Reference Point X/Y
Specify the position of the reference point. The reference point will appear in the 3D simulation area.
By Edge/corner ID Sequence
When this strategy is adopted, the vacuum gripper will pick by using the edges/corners that have been specified by the user with different priorities.
The edge/corner IDs are generated automatically in the vacuum gripper configurator. The two-digit numbers at the edge of each section are edge/corner IDs, as shown below.
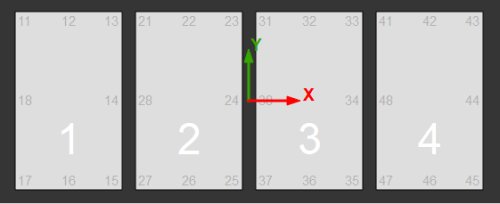
Box Surface Coverage Lower Limit
This parameter specifies the minimum proportion of a box’s upper surface covered by the vacuum gripper when the vacuum gripper attempts to pick a box. If the coverage is larger than the value, it is considered that the vacuum gripper is able to pick the box.
Fixed Edge Corner Label Numbers
Specify the sequence of the edge/corner IDs. For example, enter 11, 17, 21, and 22, and the vacuum gripper will pick by using the corresponding edge/corner according to the sequence you specified.
Suction Cup Orientation
This parameter specifies the orientation of the vacuum gripper relative to the box group during picking.
You can set the Suction Cup Long Edge Orientation and Orientation Reference, and there are four relative positional relationships in total:
-
Long edges of objects are parallel to that of the vacuum gripper.
-
Long edges of objects are perpendicular to that of the vacuum gripper.
-
The long edge of the vacuum gripper is parallel to the direction along which the boxes are grouped.
-
The long edge of the vacuum gripper is perpendicular to the direction along which the boxes are grouped.
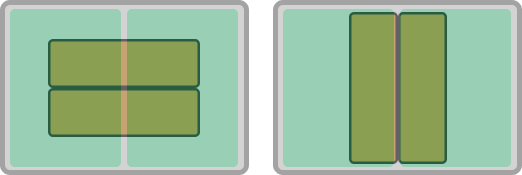
The figure on the left shows the effect when the long edge of the vacuum gripper is parallel to the long edge of the box group, and the figure on the right shows the effect when the long edge of the vacuum gripper is perpendicular to the long edge of the box group.
Carton Drop Detection
In actual box depalletizing projects, DI check points will be added to the working surface of the suction cups to monitor whether the boxes are dropped during picking and placing by comparing the sensor signal changes.
After the DI check points are added to the vacuum gripper configurator, the software will determine which sensors on the working surface of the vacuum gripper are covered by the picked boxes, and therefore the DI signals that should be detected can be confirmed.
Dist from Carton Edge To Remove DI
When DI check points are used in the carton drop detection and DI check points are at the edge of the carton, the software may mistakenly detect that the carton is dropped due to picking deviation, loose suction at the edge, deformation of the carton, or other reasons. Under such circumstances, you can set a Dist from Carton Edge To Remove DI to remove DI check points at the edge of the carton to avoid detection errors. The red frames shown in the figure below represent the edge area where the DIs are removed.
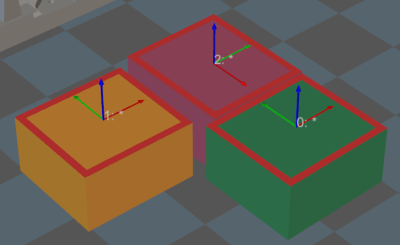
Count of Picked Workobjects
Select Limit Total Count and you can set the Planned Count and other parameters.
Planned Count |
The maximum number of total picked objects. |
Total Count of Picked |
The number of objects that have been already picked. |
Count of Picked This Time |
The number of objects picked this time. In the single-pick depalletizing scenario, this value will remain constant at 1. |
Avoid Picking on Same Workobject
This parameter group is mainly used to avoid picking on the same pick point in scenarios where the object cannot be picked successfully.
Decreased Priority Range Radius
Default value |
0 |
Instruction |
If the distance between the current pose and the most recently tried pose is less than this value, the two poses will be considered the same one, and the pose’s priority for picking will be downgraded. |
Discard Range Radius
Default value |
0 |
Instruction |
If the distance between the current pose and the lastly tried pose is less than this value, the pose will be discarded for picking. |
Example |
For example, if the robot only moves the crankshaft but fails to pick it on the first attempt, there is a possibility of successful picking on the next attempt. In this case, Decreased Priority Range Radius can be set to downgrade the priority for picking this crankshaft, while the object pose will be kept. When the robot fails to move the crankshaft at all in the first attempt, it is highly unlikely that the crankshaft can be picked successfully in the next attempt, and therefore Discard Range Radius can be set to discard the pose directly. |
Max Length of Repetition Avoidance List
Default value |
1 |
Instruction |
The maximum number of workobjects that should not be picked repeatedly. The workobject poses will form a list. When the list length exceeds the upper limit, the pose that is added to the list earliest will be removed from the list and can be used in the next round of planning. |
Example |
Assuming that the value is set to 2 and Mech-Vision outputs 3 poses when pose 1 is used and the picking fails, pose 1 will be recorded. Pose 2 will also be recorded if the picking fails. However, when pose 3 is recorded, pose 1 will be discarded, and only pose 2 and pose 3 will be kept in the avoidance list. |
Subject of Repetition Avoidance
Pick point |
Record the pick point of the workobject. If the object has 3 pick points, and one of them was recorded as used during a failed picking, the rest two will not be included in the avoidance list. |
Workobject |
Record the workobject. If the object has 3 pick points, and one of them was recorded as used during a failed picking, the rest two will be included in the avoidance list as well and the object will not be prioritized for picking next time. |