Introduction to 3D Measurement and Inspection Solution
What Is the 3D Measurement and Inspection Solution?
Based on the Mech-Eye 3D Laser Profiler and Mech-MSR 3D measurement and inspection software developed by Mech-Mind, the 3D measurement and inspection solution provides various typical 3D measurement and inspection applications such as 3D geometric measurement, height measurement, 3D defect inspection, object counting, and optical character recognition (OCR). This solution is applicable to consumer electronics, EV battery, automobile, photovoltaic, and other industries.
System Components of the 3D Measurement and Inspection Solution
The 3D measurement and inspection solution consists of the following components:
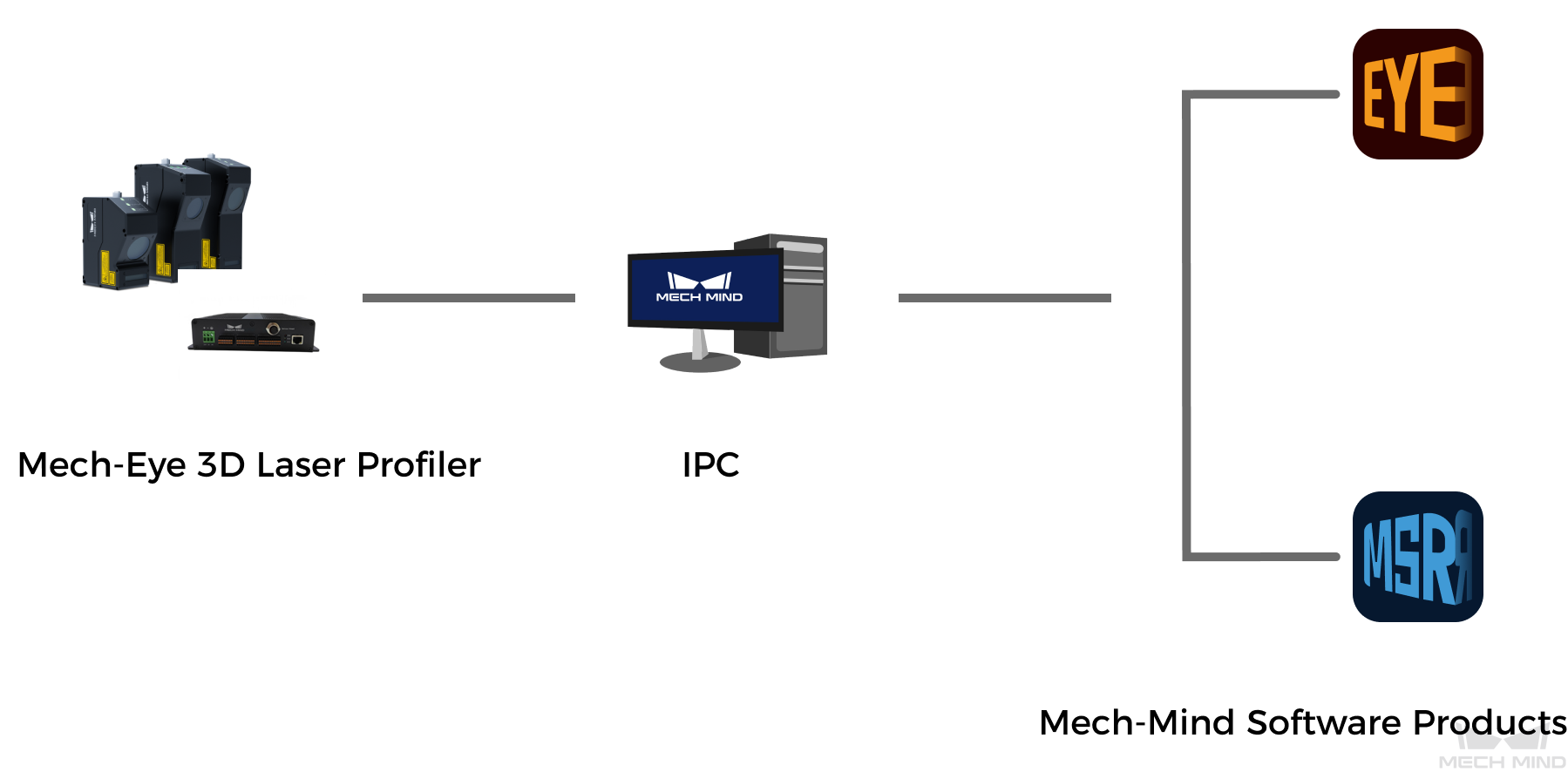
The laser profiler, IPC, and Mech-Mind’s software products (including Mech-Eye Viewer, Mech-MSR and Mech-DLK) provided by Mech-Mind constitute the Mech-Mind 3D Measurement System. |
3D Laser Profiler
Mech-Eye 3D Laser Profiler (“laser profiler”) is the 3D laser profiler developed by Mech-Mind and can output high-quality intensity images, depth maps, and point clouds. Together with Mech-MSR, it can be deployed for various 3D measurement and inspection applications.
|
Industrial Personal Computer (IPC)
The computer that provides the operating environment for the Mech-Mind’s software products.
You can use the standard IPC provided by Mech-Mind (recommended) or use your own device as the IPC. For more information about the IPC, refer to Select IPC Model.
Mech-Mind’s Software Products
Mech-Mind’s software products perform 3D measurement or inspection based on the surface data (including depth map and intensity image) acquired by the laser profiler, and output the measurement or inspection results to an external device.
The Mech-Mind 3D Measurement System mainly involves the following software:
-
Mech-Eye Viewer
Mech-Eye Viewer, installed on the IPC, is the configuration and data visualization software for laser profilers. It allows users to adjust the parameters of the laser profiler according to the characteristics of the target object, thus obtaining high-quality intensity images, depth maps, and point clouds simply and quickly.
-
Mech-MSR
Mech-MSR, installed on the IPC, is a professional 3D measurement and inspection software. It can work with the laser profiler to deploy various 3D measurement and inspection applications, such as 3D geometric measurement, height measurement, 3D defect inspection, and object counting. The software has various built-in measurement algorithms and features, and it boasts a user-friendly interface. Users can apply the software to rapidly achieve one-stop, end-to-end deployment of applications.
-
Mech-DLK
Mech-DLK, installed on the IPC, is a software product used for training deep learning models. It has integrated various powerful deep learning algorithms, such as OCR and defect detection. Through intuitive and simple UI interactions, even without programming or specialized deep learning knowledge, users can quickly implement model training and validation with this software.
Workflow of 3D Measurement and Inspection Applications
The general workflow of a 3D measurement and inspection application is shown in the figure below:
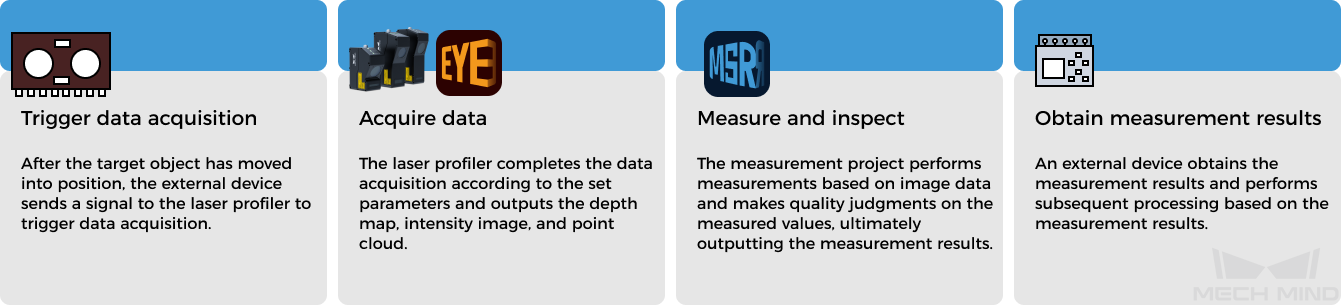
-
When the target object moves in place, an external device (such as a photoelectric sensor) sends a signal to trigger data acquisition.
-
After receiving the signal, the laser profiler acquires data of the object according to the parameters set through Mech-Eye Viewer, and generates the depth map, intensity image, and point cloud.
-
An external device triggers the measurement project to run. Mech-MSR performs measurement based on the acquired data, determines the quality of the measurement, and outputs the measurement result.
-
An external device obtains the measurement result from the 3D measurement system and performs subsequent processing based on the measurement result.
Application Scenarios of the 3D Measurement and Inspection Solution
-
3D geometric measurement
Precisely measure dimensions of targets including length, width, height, and diameter, and shape features such as flatness, roundness, and curvature. Regardless of the texture, reflectivity or color of the target object, the solution can perform stable measurements.
-
Height measurement
Measure the heights of connector pins relative to the surface of the connector. Even though the tip of the pin is extremely small, the solution can perform stable measurements.
-
Position measurement
Measure the positions of connector pins relative to the edges of the connector. Even though the tip of the pin is extremely small, the solution can perform stable measurements.
-
Bead inspection
The shape, width, height, and cross-sectional area of beads can be inspected for abnormalities such as voids, spills, bubbles, and position deviations.
-
Flatness inspection
The flatness of smartphone mid-plates is a key factor in product quality. The solution can rapidly evaluate the flatness of the mid-plates.
-
Hole locating
Quickly locate the holes on the target objects and measure the hole diameters to ensure that the shape, dimensions, and positions of the mounting holes on stamped parts are correct.
-
3D defect inspection
Extract the change points of height from the depth map, and detect the presence of defects and defect patterns such as skewness, depression, and protrusion on the surface using the height information.
-
Object counting
Count product items of different shapes and sizes in real time on high-speed production lines.