Data Processing
Data Alignment
During different scans of target objects, the object position in the acquired image data may vary slightly. You can extract common features to align different images and ensure consistency in subsequent measurements.

Follow the instructions on the Alignment Step below:
-
Select a feature region: Under Parameters of the Step’ parameter configuration panel, select the Use Feature Region option and adjust the region to include the data for feature selection and feature matching.
Once this parameter is selected, the Step will only use the data in the region to match the created model. Additionally, you should select features within the region to create a model. -
Create a model for matching: Click the Edit Model button to open the 2D model editor and select representative and common features to create a model.
-
Set Step parameters: After selecting the model, adjust the other parameters in the Parameters section of the Step. In most cases, the default settings for these parameters should be sufficient. Under Output, verify that the Surface Data item is selected.
-
Output aligned data: After the Step is run, it will output the aligned image data.

- Tuning experience
-
-
The 2D matching model is crucial to image alignment. When creating a model, you should select the edges with stable point cloud quality and low feature similarity and that can effectively determine the X or Y direction of images as features. As shown in the figure below, you can select two curved edges and a circular edge in the upper part of the smartphone midplate as features (in red) to achieve stable image alignment.
-
To shorten the cycle time of measurement, you can appropriately narrow the angle range and scale range in the “Feature parameters” panel on the right side of the 2D model editor interface. For example, if the angle deviation of the incoming target objects in images does not exceed 5°, the angle range can be set to ±5° to speed up feature matching. For more parameter details, see Feature Parameters.
-
If it is difficult to select appropriate features, you can drag the Depth range setting sliders on the right side of the image to highlight edge features for easier feature selection.
-
Now, you have completed data alignment. You can start measuring the flatness of the battery compartment’s surface.
Data Preprocessing
Data preprocessing is only required when you need to measure the height of locating holes. |
The obtained surface data contains irrelevant data and noise. To increase the stability and accuracy of data, you can filter and denoise the surface data before measurement.
Preprocessing workflow: Filtering ➡ Locating

Filtering
Use the Filter Surface Points by Normals Step to extract the data of a locating hole from aligned data and remove noise.
-
Use a feature region to select the data of the locating hole.
-
In the parameter configuration panel of the Step, adjust parameters to remove noise.
After the Step is run, it will output the processed surface data:

- Tuning experience
-
-
The Filter Surface Points by Normals Step is very effective in removing noise, especially for obtaining flat surface data. When the noise is slanted or consists of irregularly scattered points, this Step can achieve good denoising results.
-
You can adjust the Max Polar Angle parameter to filter out slanted noise of varying degrees (recommended value: 60°) and adjust the Remove Noise parameter to filter out irregular points of varying degrees. Adjusting both parameters can produce better results. For more information on the parameters, see Angle-Based Filtering.
-
Locating
Use the Locate Feature Point of Surface Step to obtain the top surface data of the locating hole from the filtered data and determine the center point for subsequent height measurement.
-
In the parameter configuration panel of the Step, select the Use Feature Region option and adjust the region to include the top surface data of the locating hole.
-
Set the “Feature Point Type” to Average to determine the center point of the top surface.
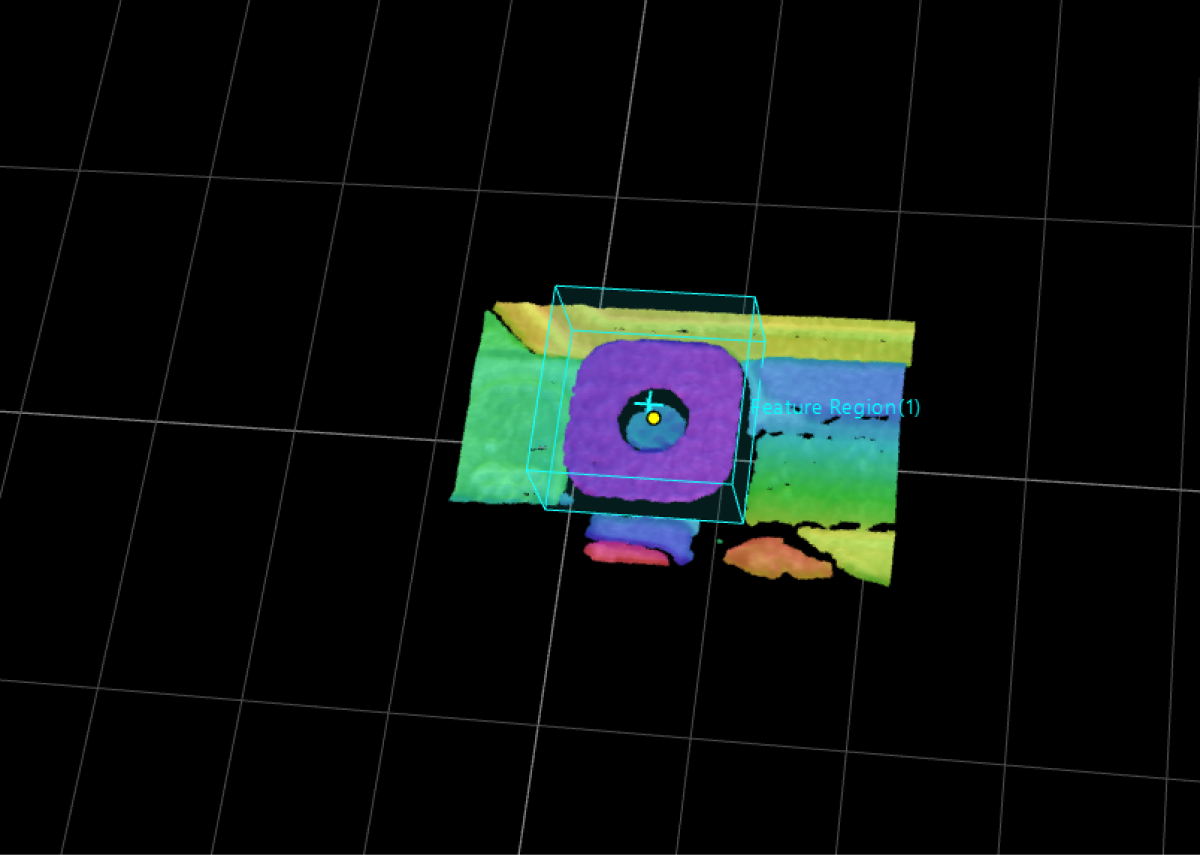
Upon this, you have finished data preprocessing.
Next, you can start measuring the flatness of the battery compartment’s surface and the height of the locating hole.