DENSO Automatic Calibration
After you set up Standard Interface communication, you can connect the robot to perform automatic calibration. The overall workflow of automatic calibration is shown in the figure below.
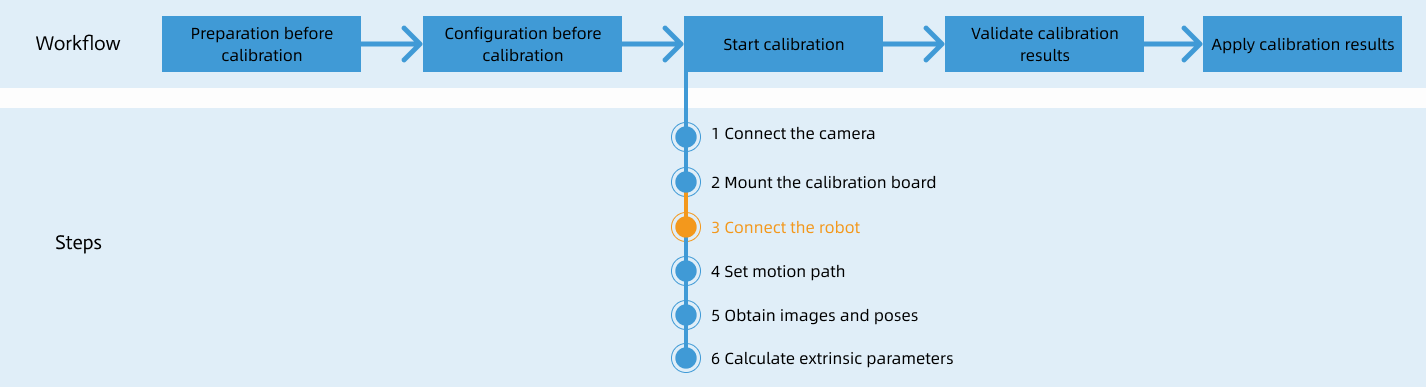
Special note
During the calibration procedure, when you reach the Connect the robot step and the Waiting for robot to connect... button appears in Mech-Vision, perform the steps below on the robot side. After you perform the steps, proceed with the remaining steps in Mech-Vision.
|
1. Select the Calibration Program
-
Turn the key of the teach pendant to MAN (the manual mode).
-
In the main interface of the teach pendant, select Program in the lower-left corner.
-
In the pop-up interface, select the MM_Auto_Calib.pcs program and then select Display.
2. Teach Calibration Start Point
-
Select the line in which the P[99] position register is located. The line in which the P[99] position register is located is shown in the figure below. After selecting the line, the blinking cursor appears somewhere in the line (the cursor may blink at different locations in the line depending on the position where the selecting operation takes place). This indicates that the line is selected.
-
The P[99] position register stores the pose of the starting point.
-
The line that includes the word Calibration displayed in the figure below indicates a calibration command where the last parameter value represents the ID of the register that holds the pose data of the calibration starting point. You can change the value of the last parameter based on actual needs. The last parameter value in this calibration command is 98, which indicates that the pose data of the calibration starting point is stored in a register with a number of 98. For details of other parameters in the calibration command, see the calibration command description.
-
-
Manually move the robot to the calibration start point.
You can use the position of the robot in the Check the Point Cloud Quality of the Calibration Board step as the calibration start point.
-
Select Get Position.
-
In the pop-up dialog box, confirm that the value of the P[99] position register is modified and then select OK.
3. Run Calibration Program
-
Turn the key of the teach pendant to AUTO (the automatic mode). Press the MOTOR key. The signal light of the MOTOR key will turn green, which indicates that the robot servo is powered on.
-
In the program interface, select Start.
-
Select Single-cycle in the pop-up dialog box and select OK.
-
When, in the Calibration window in Mech-Vision, the current status changes to connected and the button Waiting for the robot to connect... changes to Disconnect robot, click Next at the bottom.
-
Perform Step 4 of Start calibration (which is Set motion path) and the subsequent operations based the following links.
-
If the camera mounting mode is eye to hand, see this document and proceed with the relevant operations.
-
If the camera mounting mode is eye in hand, see this document and proceed with the relevant operations.
-