Online
Pallet Setting
Gap Width
The gap width (mm) between the boxes. Recommended value: 10 ~ 20mm.
Setting a minimum gap width can avoid collisions when the boxes are tightly stacked. The common causes of collisions include inaccurate dimensions or poses of the recognized boxes.
Prior Corner
This parameter specifies the corner of the pallet on which the boxes are palletized first.
Parameter | Description | Illustration |
---|---|---|
OO |
When the pallet is in the initial position, the pallet corner located in the third quadrant observed from a top-down view. |
|
OY |
Based on OO, the pallet corner in the positive Y-direction of the robot base reference frame. |
|
XY |
The corner that can be obtained by translating the OO pallet corner along both the positive X-axis and Y-axis of the robot base reference frame. |
|
XO |
Based on OO, the pallet corner in the positive X-direction of the robot base reference frame. |
Place By Drop
Enable Drop
Once this option is selected, when the held box is a certain distance away from the placing position in the Z-direction, it can be dropped directly.
When a shorter carton is placed between two taller ones or the boxes fit each other closely, the box can be placed by dropping to minimize the collision risk.
Drop Height |
Distance (mm) in the Z direction at which the object will be dropped. |
Drop Safe Margin |
The minimum distance between the side of the carton to be placed and its adjacent cartons. The unit: mm. |
In the figure below, Z denotes the drop height, and A denotes the drop safe margin.
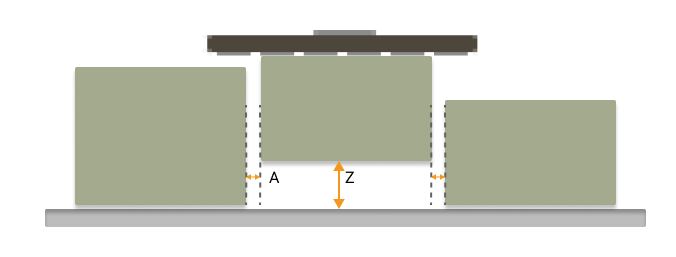
Capture Twice to Update Carton Size
Unselected by default. Select this parameter when the camera’s field of view is not large enough to capture all the scene information once and a second image is needed for scene fusion.
If the box has been picked by the “Vision Move” Step and the height of the box cannot be determined, the height of the box will be estimated when the “Mixed Case Palletizing” Step calculates the placing position and the corresponding weight, and the software can plan based on the estimated height. After capturing the box height for the second time, the “Mixed Case Palletizing” Step performs secondary planning based on the actual dimensions of the box recognized by the vision system.
This feature needs to be used in conjunction with the “Update Held Workobject” Step. |
As shown in the figure below, the robot picks the box to an image-capturing point to capture an image of it a second time, and the pose and dimensions of the box will be updated by the “Update Held Workobject” Step.
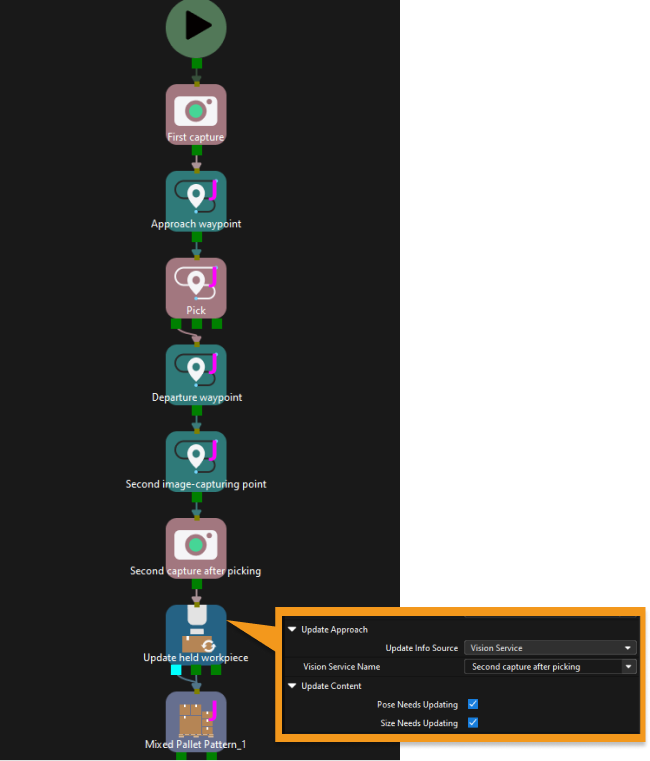
Candidates Limit
Candidate Limit Counts
This parameter is used to limit the total number of attempted box placement positions to increase the speed of subsequent path planning. For instance, if there are 20 available positions for the robot to attempt, and none of them prove feasible, 20 times of planning will be performed until it ceases, without any imposed limit. If the limit count is set to 5, the robot can stop after planning 5 times, effectively reducing the planning time. By appropriately reducing this parameter value, the planning efficiency can be improved while ensuring the accuracy of the planning.
When this parameter is set to -1, it means that there is no limit to the number of the candidate positions.
Boxes With Tags
Tag on Boundary
Unselected by default. This feature will not be used.
This feature applies to scenarios where tags are attached to the sides of the boxes and the tags must be exposed to the outside of the stack.
When the pallet is large enough and this parameter is selected, there may be only one ring of boxes stacked along the edge of the pallet, and the central space of the pallet may be idle. |
Parameters For Find Candidates
Allowed Excess
The allowable width allowed for boxes to extend beyond the edge of the pallet. Recommended value: 20 ~ 50mm.
Top-down view |
||
1: Pallet |
2: Box |
3. Distance for boxes to extend beyond the edge of the pallet |
Box Exceed Ratio
This parameter determines the maximum allowable length of the upper box beyond the plane it is pressed against.
Side view |
|
1: Length of the upper box |
2: Length of the upper box extending beyond the lower box |
Box Exceed Ratio = ②/①
Layer Height Diff
When the dimensions of the boxes on the top layer are larger than the boxes placed on the lower layer, the larger box is allowed to be placed on a plane with a height difference less than the value of this parameter.
Side view |
Sampling Rate
Sampling rate when planning the box position. Recommended value: 200, 500, 1000. The higher the sampling rate, the more accurate the pallet pattern, but the calculation speed will also be slower.
Corner Free Angle
The angle between the box entry path and the side of an adjacent box from a top-down view.
Top-down view |
If the set value is too large, a U-shaped blank area may be left after the palletizing. If the set value is too small, collisions with adjacent boxes may occur.
Recommended value: 15°~30°.
Enable Mid Point
The mid point is the center point of the box side. When a hollow is formed in the stack, the boxes can be inserted vertically into the hollow.
Safe Radius
When determining a specific corner as the entry direction, check for obstacles within a circle with the specified parameter as the radius, centered on that corner, in the XOY projection plane.
End Effector Dim Z
Height difference (mm) between the gripper bottom surface and the bottom of the second last joint of the robot in the vertical direction.
Mid Point Safe Gap
When the box is inserted to the candidate positions determined by the mid point, the minimum width (mm) of gap between adjacent boxes.
If the robot motion error and box dimension error is small, this parameter can be set to a value that is smaller than the set Gap Width, which significantly enhances the flexibility or efficiency of stacking when operating in Online mode, especially when placing a box in the middle of the stack. When the Mid Point Safe Gap is greater than the originally set Gap Width, the planning becomes infeasible. The smaller the Mid Point Safe Gap, the more available placing poses.
Scoring Weight
The parameters in this group are all scoring weights that concertedly determine the position on the pallet where the box will be placed.
Adjacent Area Weight
The greater the value, the candidate positions where the side area has more contact with the box in the stack are more likely to be selected.
Support Area Weight
The greater the value, the candidate positions where the bottom surface of the box has more contact with the upper surface of the boxes under it (i.e., larger support area) are more likely to be selected.
Base Height Weight
Base height is the difference in height between the bottom of the box to be palletized and the pallet in the Z direction. The larger the value of this parameter, the lower the target position, making it easier for boxes to be palletized to a relatively low plane.
Projected Dist to Corner Weight
The greater the value, the positions with a shorter distance projected on the pallet diagonal to the prior corner are more likely to be selected.
Support Box Num Weight
The larger the value of this parameter, the more the software will tend to select location with a larger bottom support area. This will result in a more stable pallet pattern, but a less compact stack.
Continue palletizing from loaded Info
This parameter group is used to continue palletizing on unfinished stacks.
The “Continue Palletize Info Source” parameter includes two options: FromVision, and FromAlreadyPlacedBoxes. When “FromVision” is selected, the vision project is specified to recognize pallet pattern. When “FromAlreadyPlacedBoxes” is selected, the JSON files of the stacked pallet pattern needs to be specified.