Standard Interface Commands
This section describes standard interface commands used in Mitsubishi MC communications between a KEYENCE PLC and Mech-Mind Vision System. The PLC (the client) sends commands to Mech-Mind Vision System (the server), and Mech-Mind Vision System returns the processed data to the PLC.
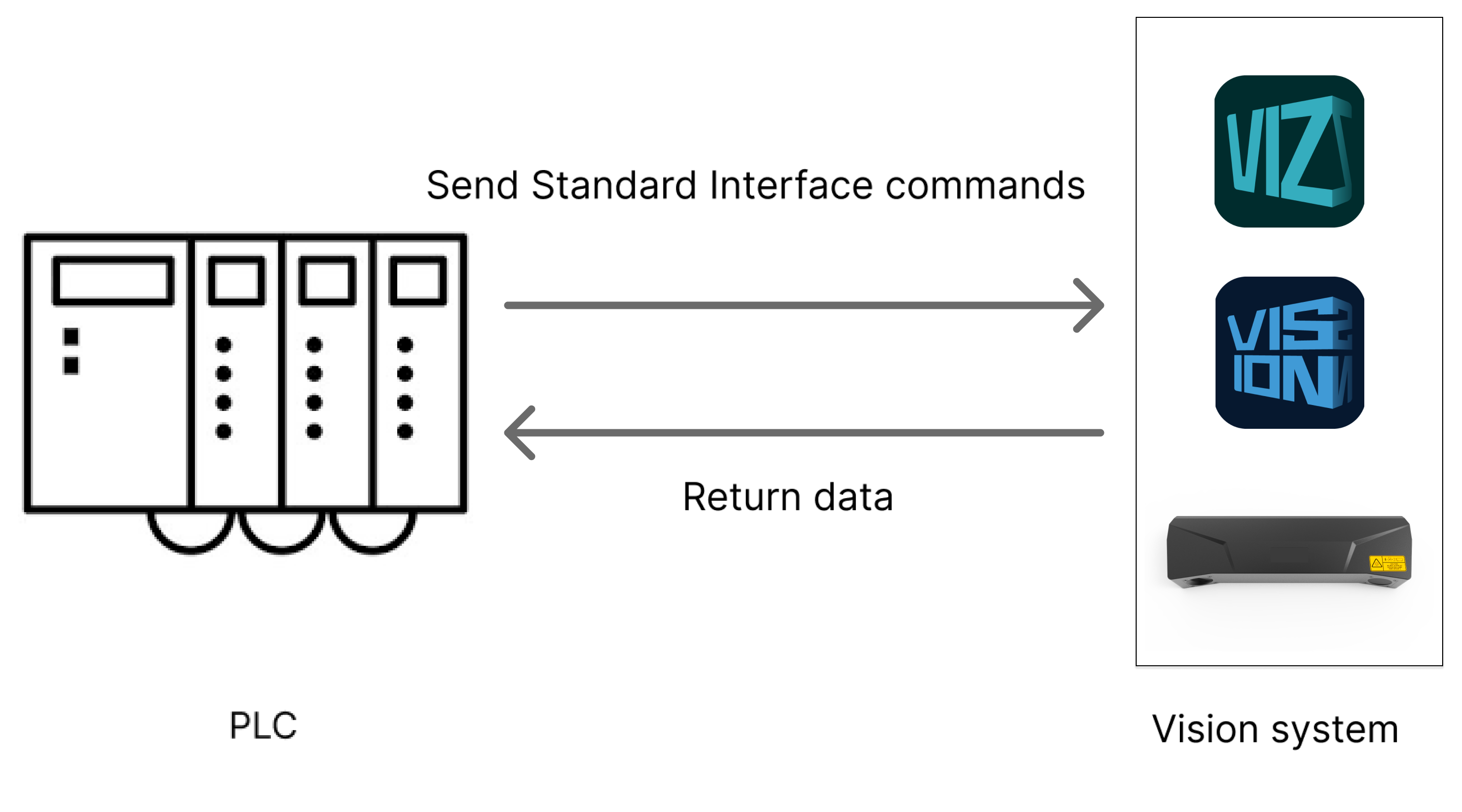
Before you call the commands, take note of the following items:
-
Unit of data:
-
The unit of joint positions is degree (°).
-
A robot’s flange pose or TCP consists of the position and pose. The position is represented in XYZ coordinates and is measured in millimeters (mm); the pose is represented in Euler angles and is measured in degrees (°).
-
-
Vision point and waypoint:
-
Vision point: An object recognized by Mech-Vision. A vision point has information including the object pose, label, velocity, dimensions, and custom data.
-
Waypoint: Each point that the robot reaches when moving along the planned path. A waypoint has information including the robot pose, label, motion type, and velocity. Waypoints can be divided into two categories:
-
Vision Move waypoint: Waypoint corresponding to the Vision Move Step.
-
Non-Vision Move waypoints, which refer to the waypoints corresponding to Move-type Steps other than the Vision Move Step.
-
-
Run Mech-Vision Project
Description
This command triggers the Mech-Vision project to run. When the Mech-Vision project is running, the vision system triggers the camera to capture images and then process the returned images with algorithms to produce a series of vision points or waypoints.
|
Calling Sequence
-
You should set Step parameters before starting a Mech-Vision project. Therefore, call Switch Mech-Vision Parameter Recipe or Input Object Dimensions to Mech-Vision Project before calling Run Mech-Vision Project.
-
Vision system gets vision points and waypoints only after a Mech-Vision project runs. Therefore, call Run Mech-Vision Project before calling Get Vision Result, Get Planned Path in Mech-Vision, or Get Mech-Vision Custom Data.
Modules
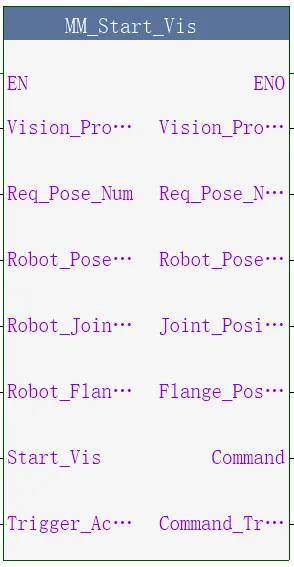
Input Parameters
Vision_Proj_Num
This parameter specifies the Mech-Vision project ID. The data type is INT. You can view the project ID of a Mech-Vision project in the Project List section of Mech-Vision. The project ID is the number before the project name.
Req_Pose_Num
This parameter specifies the expected number of vision points or waypoints to be obtained from the Mech-Vision project. The data type is INT. Value range: 0 to the largest positive integer.
If the Mech-Vision project has a Path Planning Step, this parameter specifies the expected number of waypoints. Otherwise, it specifies the expected number of vision points. |
-
0: Obtain all vision points or waypoints from the Mech-Vision project.
-
A positive integer: Obtain the specific number of vision points or waypoints from the Mech-Vision project.
-
If the total amount of vision points or waypoints output by the Mech-Vision project is smaller than the parameter value, this command will obtain the number of all vision points or waypoints.
-
If the total amount of vision points or waypoints output by the Mech-Vision project is larger than or equal to the parameter value, this command will obtain the number of vision points or waypoints as specified by this parameter.
-
|
Robot_Pose_Type
This parameter specifies the way in which the real robot pose is sent to the Mech-Vision project. The data type is INT. Valid values: 0, 1, 2, and 3. The following table describes the details.
Robot_Joint_Position
This parameter specifies the joint positions of the robot. The data type is ARRAY[0..5] OF REAL.
Robot_Flange_Pose
This parameter specifies the flange pose of the robot. The data type is ARRAY[0..5] OF REAL.
The following table explains the relationship among the Robot_Pose_Type, Robot_Joint_Position, and Robot_Flange_Pose parameters.
Robot_Pose_Type | Robot_Joint_Position | Robot_Flange_Pose | Description | Applicable scenario |
---|---|---|---|---|
0 |
0,0,0,0,0,0 |
0,0,0,0,0,0 |
The command does not send the robot pose to the Mech-Vision project. If the Path Planning Step is used in the Mech-Vision project, the start point of the planned path will be the Home point set in the path planning tool. |
This setting should be used if the camera is mounted in eye to hand mode and the project does not require images to be captured beforehand. |
1 |
Current joint positions of the robot |
Robot’s current flange pose |
The robot joint positions and flange pose must be input to the Mech-Vision project. |
This setting should be used when the camera is mounted in eye in hand mode. This setting is recommended for most scenarios except those involving gantry robots. |
2 |
0,0,0,0,0,0 |
Robot’s current flange pose |
The robot flange pose must be input to the Mech-Vision project. |
This setting is recommended for scenarios involving gantry robots. |
3 |
Custom joint positions of the robot |
0,0,0,0,0,0 |
This command sends custom joint positions to the Mech-Vision project. This joint positions will be sent to the Path Planning Step in the Mech-Vision project as the start point, where the robot will move from this start point to the first waypoint of the planned path. |
This setting should be used if the camera is mounted in eye to hand mode and the project requires images to be captured beforehand. |
Start_Vis
This parameter triggers the Mech-Vision project to start when a rising edge occurs. The data type is BOOL.
Trigger_Acknowledge
This parameter indicates whether the Command_Trigger signal successfully triggers the vision system. The data type is INT. 1 indicates that the vision system is successfully triggered, and 0 indicates that the Command_Trigger signal is not received.
Output Parameters
Vision_Proj_Num_O
This parameter indicates the Mech-Vision project ID. The data type is INT.
Req_Pose_Num_O
This parameter indicates the expected number of vision points or waypoints that are returned by the Mech-Vision project. The data type is INT. 0 indicates that all vision points or waypoints are obtained from the Mech-Vision project.
Robot_Pose_Type_O
This parameter indicates the way in which the real robot pose is sent to the Mech-Vision project. The data type is INT. Valid values: 0, 1, 2, and 3.
Joint_Position_O
This parameter indicates the joint positions of the robot. The data type is ARRAY[0..5] OF REAL.
Flange_Pose_O
This parameter indicates the flange pose of the robot. The data type is ARRAY[0..5] OF REAL.
Command
This parameter indicates the command code that will be automatically assigned. The data type is INT.
Command_Trigger
This parameter indicates the command switch that will be automatically triggered. The data type is INT.
Returned data of the MM_Camera global variable
Status_Code
This parameter stores the status code of this command. The data type is INT. If the command is successfully executed, the status code is 1102. If a command fails to be run, a specific error code is returned. For details, see Status Codes and Troubleshooting.
Example
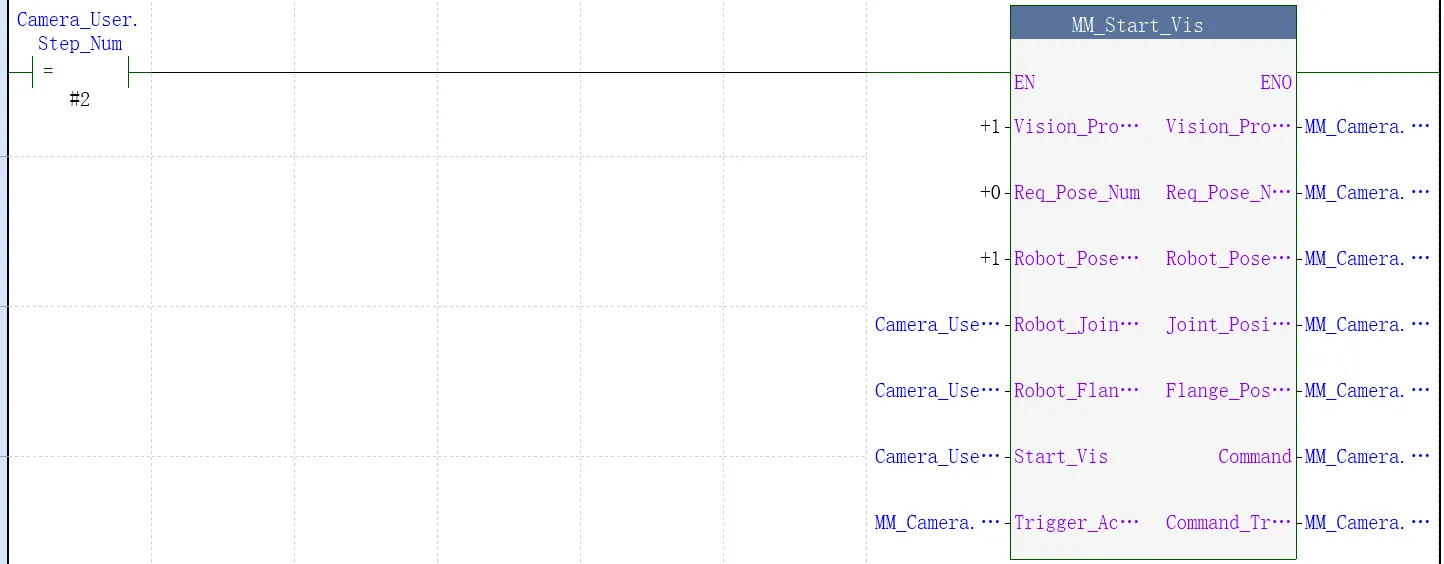
When Camera_User.Step_Num is set to 2 and Camera_User.Start_Vis is at the rising edge, the PLC triggers Mech-Vision project No.1 to run and expects Mech-Vision project No.1 to return all vision points or waypoints. At the same time, the PLC sends the current joint positions and flange pose of the robot to Mech-Vision.
Get Vision Result
Description
This command obtains vision result, namely, a series of vision points, from Mech-Vision. The object pose of the vision point (namely, the output of the poses port of the Output Step) will be automatically converted to the robot’s TCP by the vision system. The process is as follows.
If the first input port of the Output Step is Object Center Points, the Output Step will convert the object center points into the corresponding pick points. Therefore, the object poses obtained by running this command are actually poses of pick points, instead of poses of object center points. |
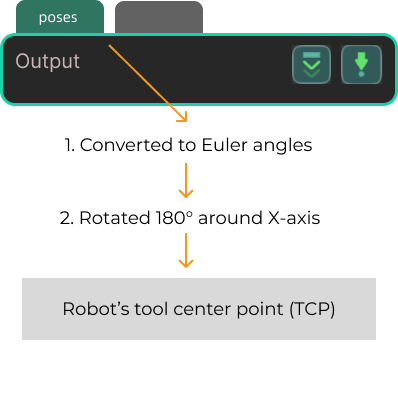
-
Convert the object pose from a quaternion to Euler angles.
-
Rotate the object’s pose around the X-axis by 180° to orient its Z-axis downward.
Calling Sequence
This command should be called after Run Mech-Vision Project.
Modules
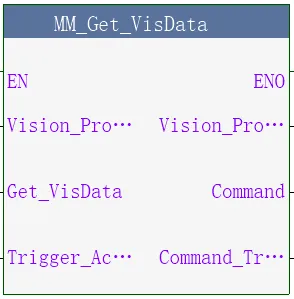
Input Parameters
Vision_Proj_Num
This parameter specifies the Mech-Vision project ID. The data type is INT. You can view the project ID of a Mech-Vision project in the Project List section of Mech-Vision. The project ID is the number before the project name.
Get_VisData
This parameter triggers the vision result to be obtained at the rising edge. The data type is BOOL.
Trigger_Acknowledge
This parameter indicates whether the Command_Trigger signal successfully triggers the vision system. The data type is INT. 1 indicates that the vision system is successfully triggered, and 0 indicates that the Command_Trigger signal is not received.
Output Parameters
Vision_Proj_Num_O
This parameter indicates the Mech-Vision project ID. The data type is INT.
Command
This parameter indicates the command code that will be automatically assigned. The data type is INT.
Command_Trigger
This parameter indicates the command switch that will be automatically triggered. The data type is INT.
Returned data of the MM_Camera global variable
Status_Code
This parameter stores the status code of this command. The data type is INT. If the command is successfully executed, the status code is 1100. If a command fails to be run, a specific error code is returned. For details, see Status Codes and Troubleshooting.
By default, after the robot sends this command, the vision system returns the result in 10 seconds. If the vision system fails to return any result in 10 seconds, a timeout error code is returned. To modify the default timeout period as needed, go to Robot and Communication > in the toolbar of Mech-Vision.![]() |
Status_of_Pose_Sent
This parameter is set to 1, which indicates that the input pose data is new. The data type is INT. After the PLC reads the pose data, please reset this parameter.
Number_of_Pose_Sent
This parameter stores the number of vision points returned by Mech-Vision. The data type is INT.
Target_Pose
This parameter indicates the poses of all vision points in the obtained vision result. The poses are TCPs. The data type is ARRAY[0..39,0..5] OF REAL.
Target_Label
This parameter indicates the labels of all vision points in the obtained vision result. Labels and poses are one-to-one paired. The data type is ARRAY[0..39] OF INT.
Switch Mech-Vision Parameter Recipe
Description
This command triggers Mech-Vision to switch the parameter recipe used by the project. The image below shows how to manually switch the parameter recipe for a Mech-Vision project. For details about parameter recipes, see the parameter recipe guide.
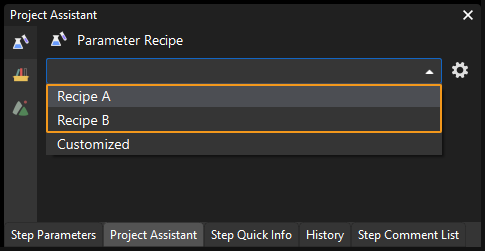
Calling Sequence
This command should be called before Run Mech-Vision Project.
Modules
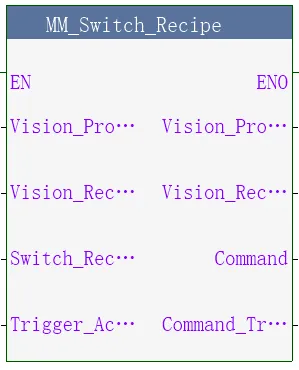
Input Parameters
Vision_Proj_Num
This parameter specifies the Mech-Vision project ID. The data type is INT. You can view the project ID of a Mech-Vision project in the Project List section of Mech-Vision. The project ID is the number before the project name.
Vision_Recipe_Num
This parameter specifies the parameter recipe ID in the Mech-Vision project. The data type is INT. For information about how to view the parameter recipe ID, see View the Parameter Recipe ID.
Switch_Recipe
This parameter triggers the switch of parameter recipe in Mech-Vision when the rising edge occurs. The data type is BOOL.
Trigger_Acknowledge
This parameter indicates whether the Command_Trigger signal successfully triggers the vision system. The data type is INT. 1 indicates that the vision system is successfully triggered, and 0 indicates that the Command_Trigger signal is not received.
Output Parameters
Vision_Proj_Num_O
This parameter indicates the Mech-Vision project ID. The data type is INT.
Vision_Recipe_Num_O
This parameter indicates the parameter recipe ID in the Mech-Vision project. The data type is INT.
Command
This parameter indicates the command code that will be automatically assigned. The data type is INT.
Command_Trigger
This parameter indicates the command switch that will be automatically triggered. The data type is INT.
Returned data of the MM_Camera global variable
Status_Code
This parameter stores the status code of this command. The data type is INT. If the command is successfully executed, the status code is 1107. If a command fails to be run, a specific error code is returned. For details, see Status Codes and Troubleshooting.
Get Planned Path in Mech-Vision
Description
This command obtains the path planned by the Mech-Vision project as a series of waypoints. The path is planned by the path planning tool, which you may enter by clicking Config wizard as shown in the image below. For details about Path Planning, see Path Planning.
Set the Port Type parameter of the Output Step in Mech-Vision to Predefined (robot path). |
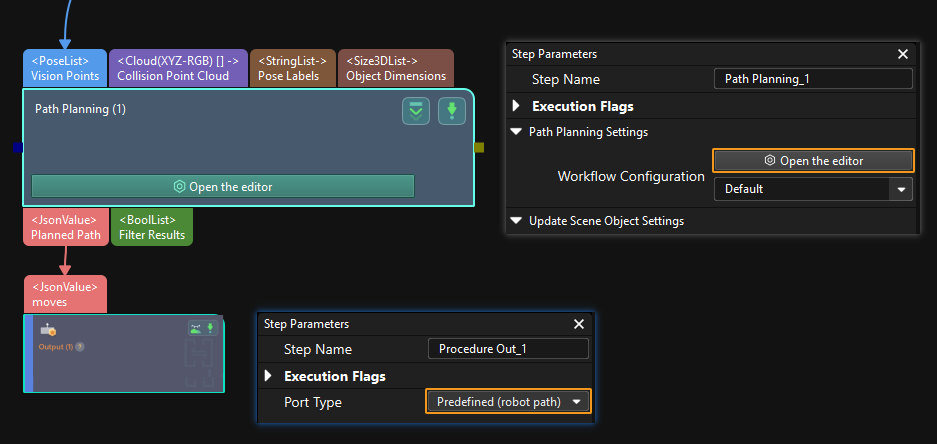
Calling Sequence
This command should be called after Run Mech-Vision Project.
Modules
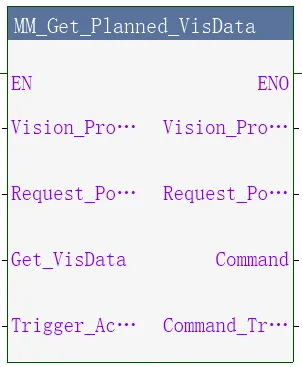
Input Parameters
Vision_Proj_Num
This parameter specifies the Mech-Vision project ID. The data type is INT. You can view the project ID of a Mech-Vision project in the Project List section of Mech-Vision. The project ID is the number before the project name.
Request_Pose_Type
This parameter specifies the type of waypoint poses to be obtained. The data type is INT. Valid values: 1 and 2.
-
1: Joint positions.
-
2: TCP.
Get_VisData
This parameter triggers the path planned by Mech-Vision to be obtained at the rising edge. The data type is BOOL.
Trigger_Acknowledge
This parameter indicates whether the Command_Trigger signal successfully triggers the vision system. The data type is INT. 1 indicates that the vision system is successfully triggered, and 0 indicates that the Command_Trigger signal is not received.
Output Parameters
Vision_Proj_Num_O
This parameter indicates the Mech-Vision project ID. The data type is INT.
Request_Pose_Type_O
This parameter indicates the pose type of the obtained waypoints. The data type is INT. 1 indicates joint positions, and 2 indicates TCP.
Command
This parameter indicates the command code that will be automatically assigned. The data type is INT.
Command_Trigger
This parameter indicates the command switch that will be automatically triggered. The data type is INT.
Returned data of the MM_Camera global variable
Status_Code
This parameter stores the status code of this command. The data type is INT. If the command is successfully executed, the status code is 1103. If a command fails to be run, a specific error code is returned. For details, see Status Codes and Troubleshooting.
By default, after the robot sends this command, the vision system returns the result in 10 seconds. If the vision system fails to return any result in 10 seconds, a timeout error code is returned. To modify the default timeout period as needed, go to Robot and Communication > in the toolbar of Mech-Vision.![]() |
Status_of_Pose_Sent
This parameter is set to 1, which indicates that the input pose data is new. The data type is INT. After the PLC reads the pose data, please reset this parameter.
Number_of_Pose_Sent
This parameter stores the number of waypoints returned by the vision system. The data type is INT. By default, the vision system can send 20 waypoints at most. As such, the maximum default value of this parameter is 20. To modify the default maximum number of poses to obtain each time as needed, go to
in the toolbar of Mech-Vision. The upper limit is 30.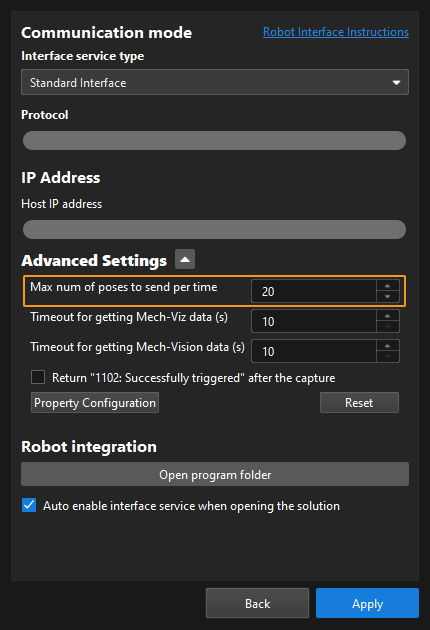
Before you call Get Planned Path in Mech-Vision, set Req_Pose_Num of Run Mech-Vision Project to 0 to reduce the number of Get Planned Path in Mech-Vision calls. If Req_Pose_Num of Run Mech-Vision Project is set to 1, only one waypoint is obtained each time you call Get Planned Path in Mech-Vision. You need to call Command 105 for several times to obtain all waypoints. |
Index_of_Vision_Picking_Point
The sequence number of the Vision Move waypoint (the waypoint corresponding to the Vision Move step of the path planning tool) in the path. The data type is INT. If the waypoint does not exist in the path, the petameter value is 0.
If the planned path consists of the following waypoints in sequence: Fixed-Point Move_1, Fixed-Point Move_2, Vision Move, and Fixed-Point Move_3, the sequence number of the Vision Move waypoint is 3.
Target_Pose
This parameter indicates the poses of all waypoints in the obtained planned path. The poses are TCPs or joint positions, depending on the Request_Pose_Type value. The data type is ARRAY[0..39,0..5] OF REAL.
Target_Label
This parameter indicates the labels of all waypoints in the obtained planned path. Labels and poses are one-to-one paired. The data type is ARRAY[0..39] OF INT.
Target_Tool_ID
This parameter indicates the tool IDs of all waypoints in the obtained planned path. The tool IDs and poses are one-to-one paired. The data type is ARRAY[0..39] OF INT.
Get Gripper DO List
Description
This command obtains the control signal list for the multi-section vacuum gripper from the Mech-Vision or Mech-Viz project. Before using this command, you must perform the following configurations in Mech-Vision or Mech-Viz.
-
Configure the Mech-Vision project
-
In the Path Planning Step, click Config wizard. In Global configuration, enable Box depalletizing.
-
In the Path Planning Step, click Config wizard, and then double-click the name of the robot tool. In the pop-up window, select Depalletizing vacuum gripper for Tool type, click Configure depalletizing vacuum gripper, and then configure DO signals according to needs.
-
-
Configure the Mech-Viz project
-
In the Vision Move Step of Mech-Viz, set Select Picking Method to Box depalletizing.
-
In Mech-Viz, double-click the tool name, select Depalletizing vacuum gripper for Tool type, click Configure depalletizing vacuum gripper, and then configure the DO signal values according to needs.
-
Calling Sequence
This command must be called before the Get Planned Path in Mech-Vision or Get Planned Path in Mech-Viz command. This means that the PLC must obtain the planned path and then obtain gripper DO signals of the Vision Move waypoint.
Modules
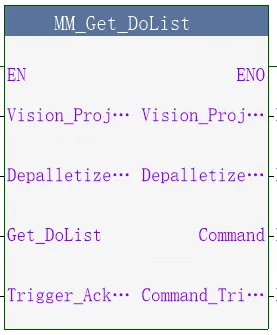
Input Parameters
Vision_Proj_Num
This parameter specifies the source of the DO signal list. The data type is INT. Value range: 0 to the largest positive integer.
-
0: Get DO signal list from Mech-Viz.
-
A positive integer: Get DO signal list from Mech-Vision. The positive integer is the Mech-Vision project ID.
Depalletize_Tool_Section_Count
This parameter indicates the number of vacuum gripper sections. The data type is INT.
Get_DoList
This parameter triggers gripper DO signals to be obtained at the rising edge. The data type is BOOL.
Trigger_Acknowledge
This parameter indicates whether the Command_Trigger signal successfully triggers the vision system. The data type is INT. 1 indicates that the vision system is successfully triggered, and 0 indicates that the Command_Trigger signal is not received.
Output Parameters
Vision_Proj_Num_O
This parameter indicates the source of the DO signal list. The data type is INT.
Depalletize_Tool_Section_Count_O
This parameter indicates the number of vacuum gripper sections. The data type is INT.
Command
This parameter indicates the command code that will be automatically assigned. The data type is INT.
Command_Trigger
This parameter indicates the command switch that will be automatically triggered. The data type is INT.
Returned data of the MM_Camera global variable
Status_Code
This parameter stores the status code of this command. The data type is INT. If the command successfully obtained the DO signal list of the Mech-Viz project, the status code is 2102. If the DO signal list is successfully obtained from Mech-Vision, the status code is 1106. If a command fails to be run, a specific error code is returned. For details, see Status Codes and Troubleshooting.
DO_LIST
This parameter indicates the 64 DO signals returned by this command. The data type is ARRAY[0..63] OF INT.
The DO signals returned by this command vary based on the deployed project.
-
Gripper DO signals planned by the Mech-Vision project
-
Under Global Configuration of the path planning tool, if Plan all vision results is disabled, this command returns 64 gripper DO signals that are planned in this round. Valid DO signals are non-negative integers ranging from 0 to 999. Invalid DO signals are -1, which serves as a placeholder.
For example, valid DO signals in the table below are 1, 3, 5, and 6, which means that the robot will set the values of these DO signals to ON.
1st
2nd
3rd
4th
5th
6th
7th
8th
…
63rd
64th
1
3
5
6
-1
-1
-1
-1
…
-1
-1
-
Under Global Configuration of the path planning tool, if Plan all vision results is enabled, Mech-Vision can perform multiple rounds of planning based on the same vision result. The 64 gripper DO signals returned by this command are obtained during all rounds of planning. In this case, you can use the number of vacuum gripper sections to differentiate the gripper DO signals obtained during each round of planning.
For example, if the number of vacuum gripper sections is 4 and the command returns 64 DO signals in total, each 4 DO signals are multi-section vacuum gripper signals obtained during each round of planning.
First round of planning
Second round of planning
…
16th round of planning
1st
2nd
3rd
4th
5th
6th
7th
8th
…
61st
62nd
63rd
64th
1
3
4
-1
1
4
-1
-1
…
-1
-1
-1
-1
-
-
Gripper DO signals planned by the Mech-Viz project
-
If Reuse Vision Result is not selected for the Vision Move Step, this command returns 64 gripper DO signals that are planned during this round. Valid DO signals are non-negative integers ranging from 0 to 999. Invalid DO signals are -1, which serves as a placeholder.
For example, valid DO signals in the table below are 1, 3, 5, and 6, which means that the robot will set the values of these DO signals to ON.
1st
2nd
3rd
4th
5th
6th
7th
8th
…
63rd
64th
1
3
5
6
-1
-1
-1
-1
…
-1
-1
-
If Reuse Vision Result is selected for the Vision Move Step and the Vision Move Step is used in a loop, Mech-Viz can perform multiple rounds of planning based on the same vision result. The 64 gripper DO signals returned by this command are obtained during all rounds of planning. In this case, you can use the number of vacuum gripper sections to differentiate the gripper DO signals obtained during each round of planning.
For example, if the number of vacuum gripper sections is 4 and the command returns 64 DO signals in total, each 4 DO signals are multi-section vacuum gripper signals obtained during each round of planning.
First round of planning
Second round of planning
…
16th round of planning
1st
2nd
3rd
4th
5th
6th
7th
8th
…
61st
62nd
63rd
64th
1
3
4
-1
1
4
-1
-1
…
-1
-1
-1
-1
-
Get Mech-Vision Custom Data
Description
This command obtains data from the custom port(s) of the “Output” Step in Mech-Vision. One command call saves all port data of the Output Step to the specified register.
Select the Output step, set Port Type to Custom, and then click Open the editor to go to the custom port configuration window. The Customized Keys section of the window displays custom port names, such as customeData1 and customeData2, as shown in the following figure.
|
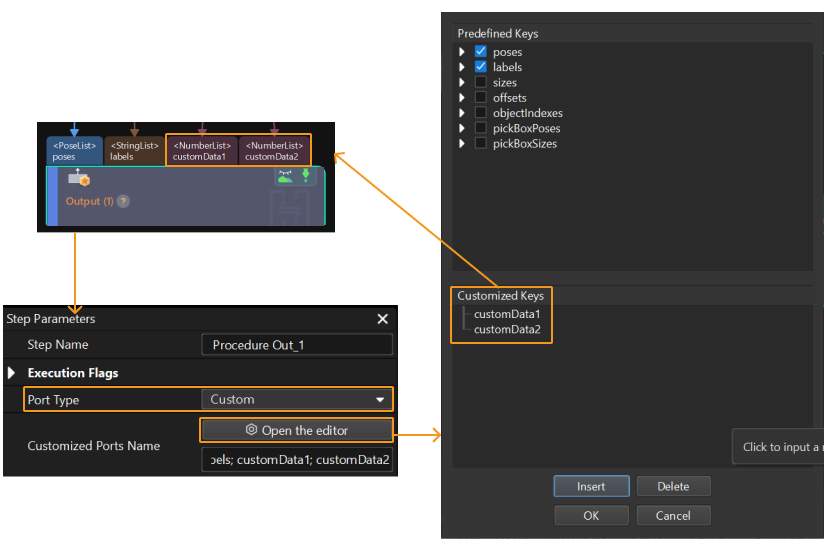
The number of custom ports cannot exceed 10. The obtained custom data is sorted in a case-sensitive alphabetical order of ports. |
Calling Sequence
This command should be called after Run Mech-Vision Project.
Modules

Input Parameters
Vision_Proj_Num
This parameter specifies the Mech-Vision project ID. The data type is INT. You can view the project ID of a Mech-Vision project in the Project List section of Mech-Vision. The project ID is the number before the project name.
Get_VisData
This parameter triggers custom data of Mech-Vision to be obtained at the rising edge. The data type is BOOL.
Trigger_Acknowledge
This parameter indicates whether the Command_Trigger signal successfully triggers the vision system. The data type is INT. 1 indicates that the vision system is successfully triggered, and 0 indicates that the Command_Trigger signal is not received.
Output Parameters
Vision_Proj_Num_O
This parameter indicates the Mech-Vision project ID. The data type is INT.
Command
This parameter indicates the command code that will be automatically assigned. The data type is INT.
Command_Trigger
This parameter indicates the command switch that will be automatically triggered. The data type is INT.
Returned data of the MM_Camera global variable
Status_Code
This parameter stores the status code of this command. The data type is INT. If the command is successfully executed, the status code is 1100. If a command fails to be run, a specific error code is returned. For details, see Status Codes and Troubleshooting.
Status_of_Pose_Sent
This parameter is set to 1, which indicates that the input pose data is new. The data type is INT. After the PLC reads the pose data, please reset this parameter.
Number_of_Pose_Sent
This parameter stores the number of vision points returned by Mech-Vision. The data type is INT.
Target_Pose
This parameter indicates the poses of all vision points in the obtained vision result. The poses are TCPs. The data type is ARRAY[0..39,0..5] OF REAL.
Target_Label
This parameter indicates the labels of all vision points in the obtained vision result. Labels and poses are one-to-one paired. The data type is ARRAY[0..39] OF INT.
Custom_Vision_Output
This parameter indicates the custom data of each vision point in the obtained vision result. Custom data and poses are one-to-one paired. The data type is ARRAY[0..39,0..9] OF REAL.
Run Mech-Viz project
Description
This command triggers the Mech-Viz project to run. Mech-Viz plans the robot’s motion path based on the vision result output by Mech-Vision.
Right-click the project name in the project resource panel in Mech-Viz and select Autoload Project. |
Modules
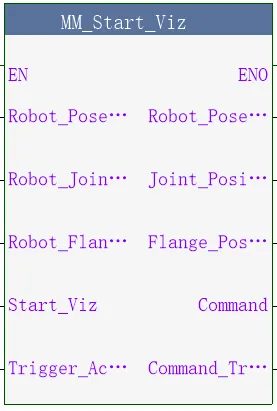
Input Parameters
Robot_Pose_Type
This parameter specifies the way in which the real robot pose is sent to the Mech-Viz project. Valid values: 0, 1, and 2. The following table describes the details. The data type is INT.
Robot_Joint_Position
This parameter specifies the joint positions of the robot. The data type is ARRAY[0..5] OF REAL.
Robot_Flange_Pose
This parameter specifies the flange pose of the robot. The data type is ARRAY[0..5] OF REAL.
The following table explains the relationship among the Robot_Pose_Type, Robot_Joint_Position, and Robot_Flange_Pose parameters.
Robot_Pose_Type | Robot_Joint_Position | Robot_Flange_Pose | Description | Applicable scenario |
---|---|---|---|---|
0 |
0,0,0,0,0,0 |
0,0,0,0,0,0 |
The command does not need to send the robot pose to the Mech-Viz project. The simulated robot in Mech-Viz moves from the initial pose (joint positions = [0, 0, 0, 0, 0, 0]) to the first waypoint. |
This setting is recommended when the camera is mounted in the Eye To Hand method. |
1 |
Current joint positions of the robot |
Robot’s current flange pose |
In this command, the robot sends its current joint positions and flange pose to the Mech-Viz project. The simulated robot in Mech-Viz moves from the input joint positions to the first waypoint. |
This setting is recommended when the camera is mounted in the Eye In Hand method. |
2 |
Joint positions of the start point of the planned path |
0,0,0,0,0,0 |
In this command, the robot sends the joint positions of a teach point (the custom joint positions), instead of the current joint positions, to the Mech-Viz project. The Mech-Viz project uses the input joint positions to plan the next path in advance while the robot is not in the camera capture region, as shown below. The simulated robot in Mech-Viz moves from the input joint positions to the first waypoint. |
This setting is recommended when the camera is mounted in the Eye To Hand method. |
If the camera is mounted in the Eye To Hand method, option 2 recommended for Robot_Pose_Type. Why?
In the Eye To Hand method, the camera can perform image capturing for the next round of path planning before the robot returns to the image capture region and picking region, thus shortening the cycle time. The image below demonstrates how a robot works in the placing region.
If Robot_Pose_Type is set to 1, the robot will send the current pose to Mech-Viz. It is possible that the real robot moves to other positions before reaching the first waypoint. However, the simulated robot moves directly to the first waypoint of the Mech-Viz project from the pose sent by the robot. Consequently, there may be a mismatch between the paths of the real robot and simulated robot. This mismatch can potentially lead to unpredicted safety hazards, especially if collision is detected in the path of the simulated robot.
On the other hand, if Robot_Pose_Type is set to 2, the robot will send the image-capturing pose set by teaching to Mech-Viz. Thus, the real robot can trigger the next round of path planning in Mech-Viz when the real robot is in the image-capturing region and the cycle time can be shortened.
In conclusion, Robot_Pose_Type should be set to 2 for projects in the Eye To Hand method.
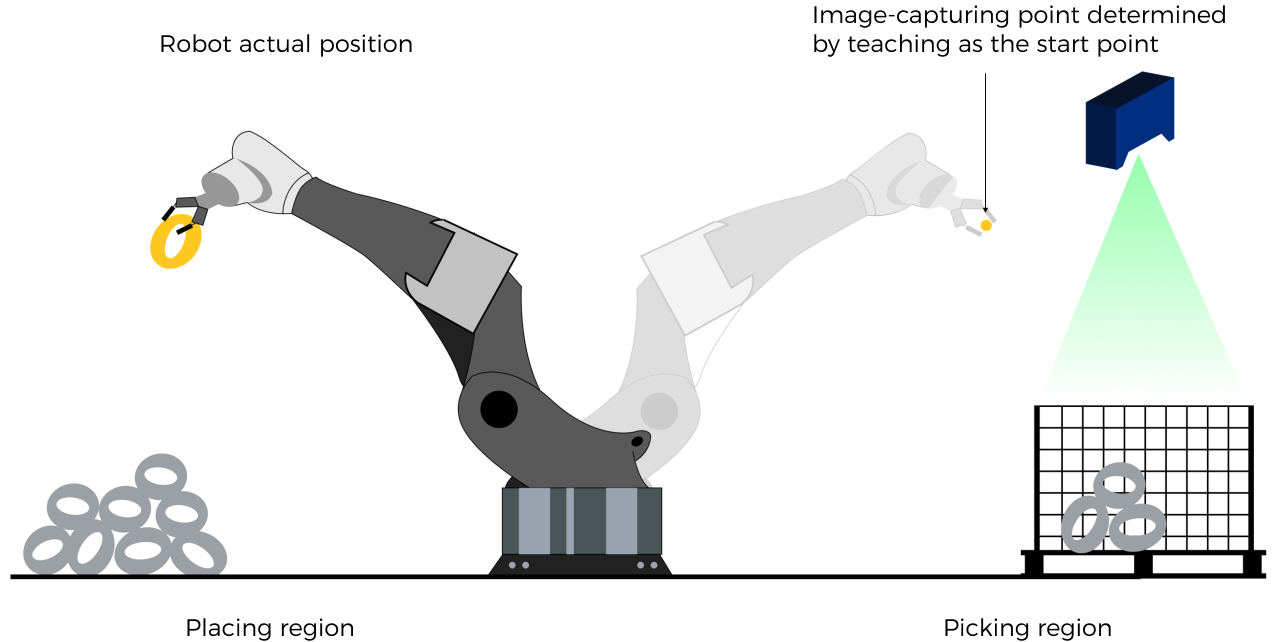
Start_Viz
This parameter triggers the Mech-Viz project to run at the rising edge. The data type is BOOL.
Trigger_Acknowledge
This parameter indicates whether the Command_Trigger signal successfully triggers the vision system. The data type is INT. 1 indicates that the vision system is successfully triggered, and 0 indicates that the Command_Trigger signal is not received.
Output Parameters
Robot_Pose_Type_O
This parameter indicates the way in which the real robot pose is sent to the Mech-Vision project. The data type is INT. Valid values: 0, 1, and 2.
Joint_Position_O
This parameter indicates the joint positions of the robot. The data type is ARRAY[0..5] OF REAL.
Flange_Pose_O
This parameter indicates the flange pose of the robot. The data type is ARRAY[0..5] OF REAL.
Command
This parameter indicates the command code that will be automatically assigned. The data type is INT.
Command_Trigger
This parameter indicates the command switch that will be automatically triggered. The data type is INT.
Returned data of the MM_Camera global variable
Status_Code
This parameter stores the status code of this command. The data type is INT. If the command is successfully executed, the status code is 2103. If a command fails to be run, a specific error code is returned. For details, see Status Codes and Troubleshooting.
Stop Mech-Viz Project
Calling Sequence
This command should be called after Run Mech-Viz project.
Modules
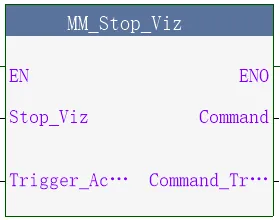
Input Parameters
Stop_Viz
This parameter triggers the Mech-Viz project to stop at the rising edge. The data type is BOOL.
Trigger_Acknowledge
This parameter indicates whether the Command_Trigger signal successfully triggers the vision system. The data type is INT. 1 indicates that the vision system is successfully triggered, and 0 indicates that the Command_Trigger signal is not received.
Output Parameters
Command
This parameter indicates the command code that will be automatically assigned. The data type is INT.
Command_Trigger
This parameter indicates the command switch that will be automatically triggered. The data type is INT.
Returned data of the MM_Camera global variable
Status_Code
This parameter stores the status code of this command. The data type is INT. If the command is successfully executed, the status code is 2104. If a command fails to be run, a specific error code is returned. For details, see Status Codes and Troubleshooting.
Set the exit port for the Branch by Msg Step in Mech-Viz
Description
This command sets the exit port for the Branch by Msg Step. When the next Step is a Branch by Msg Step, the Mech-Viz project will wait for this command to specify the exit port.
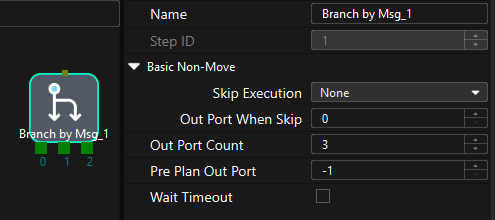
Calling Sequence
This command should be called after Run Mech-Viz project.
Modules
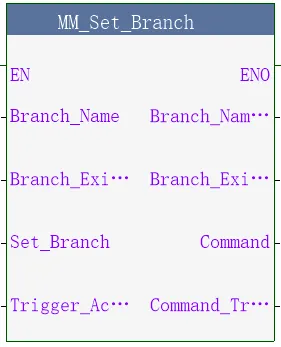
Input Parameters
Branch_Name
This parameter specifies the Step ID of the Branch by Msg Step. The data type is INT. The value is a positive integer. The Step ID is displayed in the Step parameter panel. For example, the Step ID of the Step in the image above is 1.
Branch_Exit_Port
This parameter specifies the exit port ID of the Branch by Msg Step. The data type is INT. The value is a positive integer. When the parameter value is set to N, the Mech-Viz project exits from the port with an ID of N-1 of the Branch by Msg Step.
Set_Branch
This parameter triggers the exit port of the Branch by Msg Step to be set in the Mech-Viz project at the rising edge. The data type is BOOL.
Trigger_Acknowledge
This parameter indicates whether the Command_Trigger signal successfully triggers the vision system. The data type is INT. 1 indicates that the vision system is successfully triggered, and 0 indicates that the Command_Trigger signal is not received.
Output Parameters
Branch_Name_O
This parameter indicates the Step ID of the Branch by Msg Step. The data type is INT.
Branch_Exit_Port_O
This parameter indicate the exit port of the Branch by Msg Step. The data type is INT.
Command
This parameter indicates the command code that will be automatically assigned. The data type is INT.
Command_Trigger
This parameter indicates the command switch that will be automatically triggered. The data type is INT.
Returned data of the MM_Camera global variable
Status_Code
This parameter stores the status code of this command. The data type is INT. If the command is successfully executed, the status code is 2105. If a command fails to be run, a specific error code is returned. For details, see Status Codes and Troubleshooting.
Set Current Index in Mech-Viz
Description
This command sets the value of the Current Index parameter of index-type Steps. Index-type Steps are Steps that include the Index section, which include Move by Grid, Move by List, Custom Pallet Pattern, and Predefined Pallet Pattern.
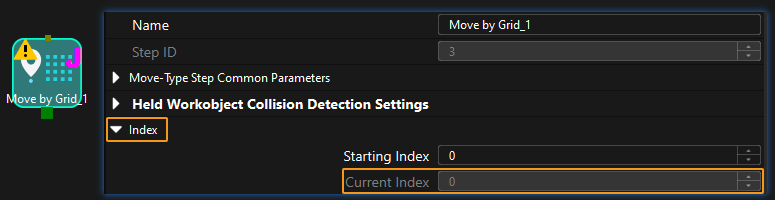
Calling Sequence
Index-type Steps are often preceded by a Branch by Msg Step. The PLC should call commands in this order: Run Mech-Viz project, Set Current Index in Mech-Viz, and Set the exit port for the Branch by Msg Step in Mech-Viz. This is to ensure that Mech-Viz has enough time to set the Current Index value.
Modules
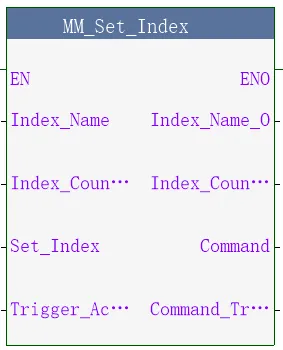
Input Parameters
Index_Name
This parameter specifies the Step ID of the Index-type Step. The data type is INT. The value is a positive integer. The Step ID is displayed in the Step parameter panel. For example, the Step ID of the Step in the image above is 3.
Index_Counter
This parameter specifies the current index for a Index-type Step. The data type is INT. The value is a positive integer. When this parameter value is set to N, the current index of the corresponding Step is N-1.
Set_Index
This parameter triggers the Current Index value to be set in the Mech-Viz project at the rising edge. The data type is BOOL.
Trigger_Acknowledge
This parameter indicates whether the Command_Trigger signal successfully triggers the vision system. The data type is INT. 1 indicates that the vision system is successfully triggered, and 0 indicates that the Command_Trigger signal is not received.
Output Parameters
Index_Name_O
This parameter indicates the Step ID of the index-type Step. The data type is INT.
Index_Counter_O
This parameter indicates the Current Index value of the index-type Step. The data type is INT.
Command
This parameter indicates the command code that will be automatically assigned. The data type is INT.
Command_Trigger
This parameter indicates the command switch that will be automatically triggered. The data type is INT.
Returned data of the MM_Camera global variable
Status_Code
This parameter stores the status code of this command. The data type is INT. If the command is successfully executed, the status code is 2106. If a command fails to be run, a specific error code is returned. For details, see Status Codes and Troubleshooting.
Get Planned Path in Mech-Viz
Description
This command obtains the path planned by the Mech-Viz project as a series of waypoints.
Waypoint: Each point that the robot reaches when moving along the planned path. A waypoint has information including the robot pose, label, motion type, and velocity. Waypoints can be divided into two categories:
|
Calling Sequence
This command should be called after Run Mech-Viz project.
Modules
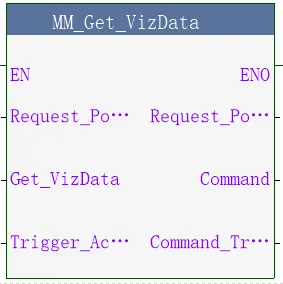
Input Parameters
Request_Pose_Type
This parameter specifies the type of waypoint poses to be obtained. The data type is INT. Valid values: 1 and 2.
-
1: Joint positions.
-
2: TCP.
Get_VizData
This parameter triggers the path planned by Mech-Viz to be obtained at the rising edge. The data type is BOOL.
Trigger_Acknowledge
This parameter indicates whether the Command_Trigger signal successfully triggers the vision system. The data type is INT. 1 indicates that the vision system is successfully triggered, and 0 indicates that the Command_Trigger signal is not received.
Output Parameters
Request_Pose_Type_O
This parameter indicates the pose type of the obtained waypoints. The data type is INT. 1 indicates joint positions, and 2 indicates TCP.
Command
This parameter indicates the command code that will be automatically assigned. The data type is INT.
Command_Trigger
This parameter indicates the command switch that will be automatically triggered. The data type is INT.
Returned data of the MM_Camera global variable
Status_Code
This parameter stores the status code of this command. The data type is INT. If the command is successfully executed, the status code is 2100. If a command fails to be run, a specific error code is returned. For details, see Status Codes and Troubleshooting.
By default, after the robot sends this command, the vision system returns the result in 10 seconds. If the vision system fails to return any result in 10 seconds, a timeout error code is returned. To modify the default timeout period as needed, go to Robot and Communication > in the toolbar of Mech-Vision.![]() |
Status_of_Pose_Sent
This parameter is set to 1, which indicates that the input pose data is new. The data type is INT. After the PLC reads the pose data, please reset this parameter.
Number_of_Pose_Sent
This parameter stores the number of waypoints that are returned by the vision system. By default, the vision system sends no more than 20 waypoints at a time. Therefore, the maximum default value of this parameter is 20. To modify the default maximum number of poses to obtain each time as needed, go to
in the toolbar of Mech-Vision. The upper limit is 30.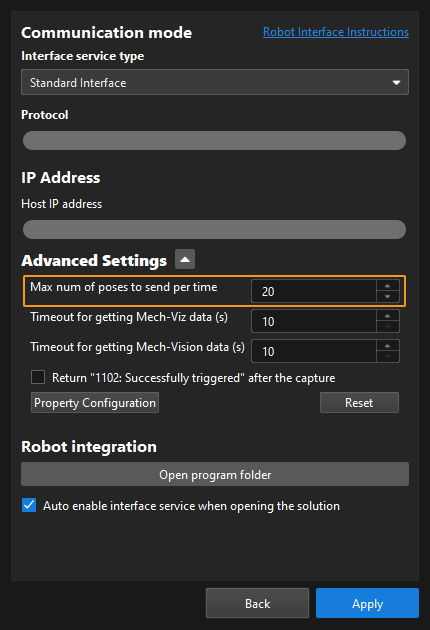
Index_of_Vision_Picking_Point
The sequence number of the Vision Move waypoint (i.e., the waypoint corresponding to the Vision Move Step in the Mech-Viz project) in the path. The data type is INT. If the waypoint does not exist in the path, the petameter value is 0.
If the planned path consists of the following waypoints in sequence: Fixed-Point Move_1, Fixed-Point Move_2, Vision Move, and Fixed-Point Move_3, the sequence number of the Vision Move waypoint is 3.
Target_Pose
This parameter indicates the poses of all waypoints in the obtained planned path. The poses are TCPs or joint positions, depending on the Request_Pose_Type value. The data type is ARRAY[0..39,0..5] OF REAL.
Target_Label
This parameter indicates the labels of all waypoints in the obtained planned path. Labels and poses are one-to-one paired. The data type is ARRAY[0..39] OF INT.
Target_Tool_ID
This parameter indicates the tool IDs of all waypoints in the obtained planned path. The tool IDs and poses are one-to-one paired. The data type is ARRAY[0..39] OF INT.
Input Object Dimensions to Mech-Vision Project
Description
This command dynamically inputs object dimensions into the Mech-Vision project. The object dimensions are the values of the Box Size Settings parameters in the Read Object Dimensions Step.
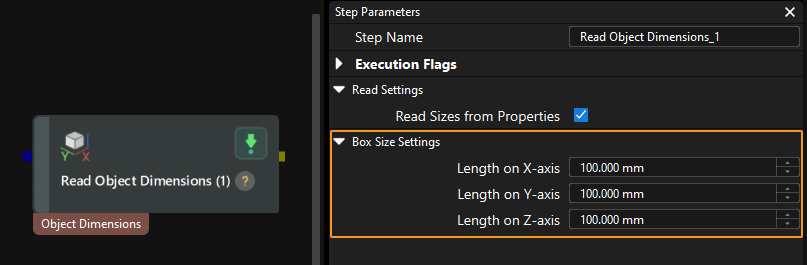
Calling Sequence
This command should be called before Run Mech-Vision Project.
Modules
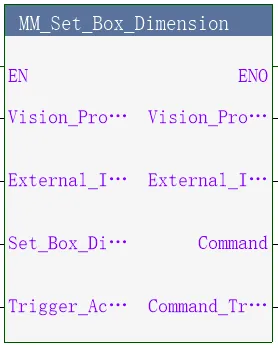
Input Parameters
Vision_Proj_Num
This parameter specifies the Mech-Vision project ID. The data type is INT. You can view the project ID of a Mech-Vision project in the Project List section of Mech-Vision. The project ID is the number before the project name.
External_Input_Box_Dimension
This parameter inputs the length, width, and height of the object to the Mech-Vision project. The length, width, and height are measured in millimeters (mm). These values are read by the Read Object Dimensions Step and set for the parameters Length on X-axis, Length on Y-axis and Length on Z-axis. The data type is ARRAY[0..2] OF REAL.
Set_Box_Dimension
This parameter triggers the object dimensions to be input to the Mech-Vision project at the rising edge. The data type is BOOL.
Trigger_Acknowledge
This parameter indicates whether the Command_Trigger signal successfully triggers the vision system. The data type is INT. 1 indicates that the vision system is successfully triggered, and 0 indicates that the Command_Trigger signal is not received.
Output Parameters
Vision_Proj_Num_O
This parameter indicates the Mech-Vision project ID. The data type is INT.
External_Input_Box_Dimension_O
This parameter indicates the object dimensions input to the Mech-Vision project. The data type is ARRAY[0..2] OF REAL.
Command
This parameter indicates the command code that will be automatically assigned. The data type is INT.
Command_Trigger
This parameter indicates the command switch that will be automatically triggered. The data type is INT.
Returned data of the MM_Camera global variable
Status_Code
This parameter stores the status code of this command. The data type is INT. If the command is successfully executed, the status code is 1108. If a command fails to be run, a specific error code is returned. For details, see Status Codes and Troubleshooting.
Get Message from Notify Step
Description
When the Mech-Vision project or Mech-Viz project is executing the Notify Step, the vision system returns the message predefined in the Notify Step.
When the Notify Step is executed in the Mech-Vision or Mech-Viz project, the message remains in the buffer of the vision system for only one second. Therefore, you should consider the timing of calling this command to ensure successful message retrieval. Additionally, after receiving the message, the PLC should clear the data in the register. |
Before sending this command, complete the following settings for the Notify Step:
-
For a Notify Step in the Mech-Vision project:
-
Connect the Notify Step to the right side of another Step. The Output Step is used in the example in the image below.
-
Select Trigger Control Flow Given Output in the parameter panel of the Output Step.
-
In the parameter panel of the Notify Step, enter Standard Interface Notify (the value cannot be modified) for Service Name. Enter a positive integer for Message, for example, 1001.
-
-
For a Notify Step in the Mech-Viz project:
-
Connect the Notify Step to a proper Step in the workflow.
-
In the parameter panel of the Notify Step, select Standard Interface. Enter a positive integer for Message, for example, 1000.
-
Calling Sequence
This command should be called after Run Mech-Vision Project or Run Mech-Viz project.
Modules
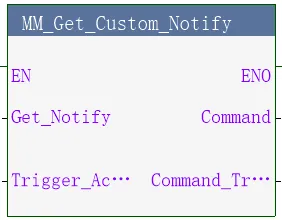
Input Parameters
Get_Notify
This parameter triggers the message of the Notify Step to be obtained at the rising edge. The data type is BOOL.
Trigger_Acknowledge
This parameter indicates whether the Command_Trigger signal successfully triggers the vision system. The data type is INT. 1 indicates that the vision system is successfully triggered, and 0 indicates that the Command_Trigger signal is not received.
Example
For example, the message set in the Notify Step is 777, and the PLC is obtaining a message in the automatic mode.
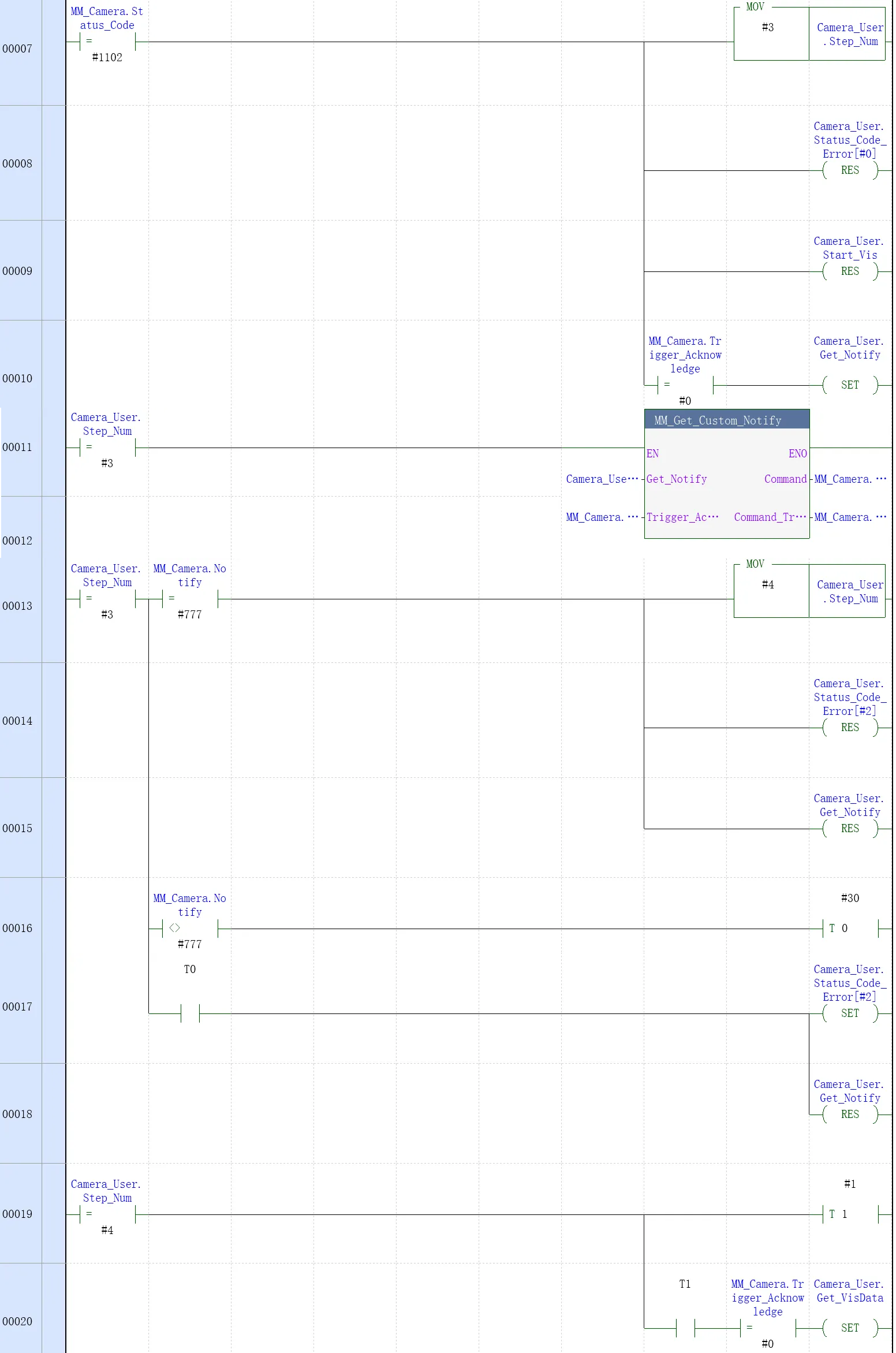
In this example, whenCamera_User.Step_Num is set to 3 in the automatic mode, the value of MM_Camera.Notify is not 777. After MM_Get_Custom_Notify is enabled when the Camera_User.Get_Notify variable is at the rising edge, the program retrieves the message from the Notify Step. If the message retrieval was successful, the value of MM_Camera.Notify changes to 777. If the value remains unchanged, the PLC will prompt an error after 3 seconds.
Get Project Status
Modules
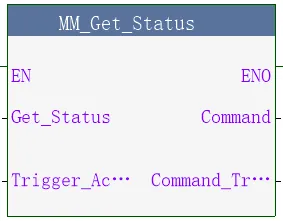
Input Parameters
Get_Status
This parameter checks if the Mech-Vision project is ready at the rising edge. The data type is BOOL.
Trigger_Acknowledge
This parameter indicates whether the Command_Trigger signal successfully triggers the vision system. The data type is INT. 1 indicates that the vision system is successfully triggered, and 0 indicates that the Command_Trigger signal is not received.
Output Parameters
Command
This parameter indicates the command code that will be automatically assigned. The data type is INT.
Command_Trigger
This parameter indicates the command switch that will be automatically triggered. The data type is INT.
Returned data of the MM_Camera global variable
Status_Code
This parameter stores the status code of this command. The data type is INT. If the command is successfully executed, the status code is 1101. If a command fails to be run, a specific error code is returned. For details, see Status Codes and Troubleshooting.
Clear Data
Modules
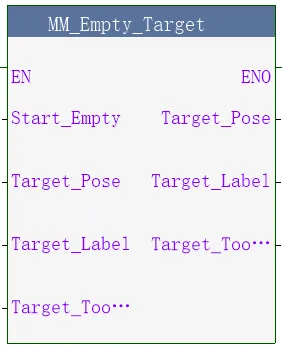
Input Parameters
Start_Empty
This parameter triggers the obtained poses, labels, and tool IDs to be cleared. This parameter will take effect when it is set. The data type is BOOL.
Trigger_Acknowledge
This parameter indicates whether the Command_Trigger signal successfully triggers the vision system. The data type is INT. 1 indicates that the vision system is successfully triggered, and 0 indicates that the Command_Trigger signal is not received.
Input/Output Parameters
Target_Pose
This parameter indicates the poses of the obtained waypoints or vision points. The data type is ARRAY[0..39,0..5] OF REAL.
Target_Label
This parameter indicates the labels of the obtained waypoints or vision points. The data type is ARRAY[0..39] OF INT.
Target_Tool_ID
This parameter indicates the tool IDs of the obtained waypoints or vision points. The data type is ARRAY[0..39] OF INT.