Approach to Ensuring Qualified Picking Accuracy
Throughout the practical application deployment stages, you need to take targeted accuracy improvement measures to reduce possible errors. This ensures that the picking accuracy aligns with the project requirements.
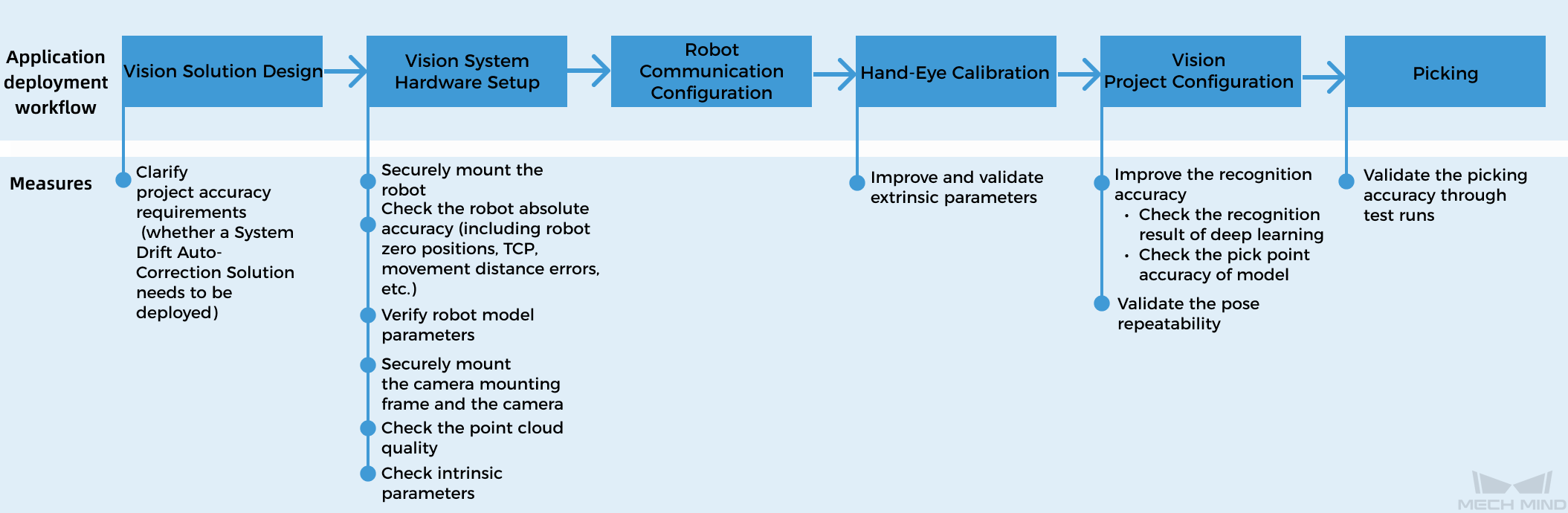
The accuracy improvement measures that should be taken at each stage of deployment are described below.
Deployment stage | Improvement measure | Description |
---|---|---|
1. Vision Solution Design |
Clarify project accuracy requirements. |
Before deploying the application, establish the accuracy requirements it must meet. For scenarios requiring high accuracy, confirm whether a System Drift Self-Correction solution needs to be deployed. |
2. Vision System Hardware Setup |
Securely mount the robot. |
Insecure mounting of the robot can impact its repeatability. |
Check the robot absolute accuracy. |
Check whether any of the zero positions of the robot is missing, check the movement distance error, and confirm the TCP accuracy. |
|
Verify robot model parameters. |
If the robot model parameters are inaccurate, it will lead to inaccurate waypoints output by the vision system, and even lead to collisions. |
|
Securely mount the camera mounting frame and camera. |
Insecure mounting of the camera mounting frame and camera can compromise the camera’s absolute accuracy and repeatability. |
|
Check the point cloud quality. |
Poor point cloud quality affects vision recognition accuracy. |
|
Check intrinsic parameters. |
Ensure that the camera intrinsic parameters are qualified for use. |
|
3. Robot Communication Configuration |
/ |
/ |
4. Hand-Eye Calibration |
Improve and validate extrinsic parameters. |
Large errors in extrinsic parameters can increase picking pose errors. After hand-eye calibration, check the accuracy of extrinsic parameters. |
5. Vision Project Configuration |
Improve the recognition accuracy. |
The selection of the recognition algorithm and the accuracy of the point cloud model and pick points impact pose accuracy. |
Validate the pose repeatability. |
After configuring the vision project, validate the repeatability of poses output by the vision project. |
|
6. Picking |
Validate the picking accuracy through test runs. |
Before deploying the vision system on the production line, conduct test runs to verify picking accuracy. |
Next, you can follow the improvement measures to improve the overall picking accuracy of your application.