方案常见问题
本节介绍单品类麻袋拆垛方案的常见问题、可能的原因及解决方法。
问题二:深度学习识别无结果
可能原因
-
采集 2D 图时,曝光时间设置不合理。如下图所示,从左至右分别为曝光时间过长、曝光时间正常、曝光时间过短时的图像。
-
采集 2D 图时,相机白平衡设置不合理。如下图所示,左图为白平衡未设置不合理时的图像,右图为白平衡设置正常时的图像。
-
深度学习识别区域(2D ROI)设置不合理。
-
深度学习模型对此类型麻袋兼容性较差,需迭代深度学习模型。
解决方法
-
调整相机曝光时间,确保采集到的 2D 图正常。
-
调整相机白平衡,调整方法可参考 调节白平衡 。
-
重新设置 2D ROI。需保证设置的 2D ROI 包含整个托盘上表面,且 ROI 需要比满垛时的垛型稍大一圈,同时 ROI 内尽量不包含其它干扰点云。
-
采集麻袋图像数据,对深度学习模型进行迭代。
问题三:位姿调整结果异常
可能原因
-
3D ROI 内未包含完整的麻袋,在后续处理过程中无法进行麻袋尺寸校验,导致Mech-Vision工程无输出。
-
深度学习未正确分割出单个麻袋掩膜,在后续处理过程中无法进行尺寸校验,导致Mech-Vision工程无输出。
-
在识别麻袋中心位姿步骤组合中输入的麻袋尺寸与识别到的麻袋尺寸差异较大,无法进行尺寸校验,导致Mech-Vision工程无输出。
-
位姿防错过当,去除了正确的麻袋位姿,导致Mech-Vision工程无输出。
解决方法
-
根据工作站布局和垛型尺寸重新设置 3D ROI,使麻袋不超出 ROI。
-
双击进入深度学习分割单个麻袋掩膜步骤组合,查看深度学习模型包推理步骤的可视化输出结果,若可视化输出结果中存在麻袋不完整或漏识别的情况,可参考问题二进行解决。
-
测量麻袋尺寸,并与输入的尺寸进行对比。若尺寸差异过大,可在识别麻袋中心位姿步骤组合的读取物体尺寸步骤参数处重新设置麻袋尺寸。
-
选中调整位姿步骤组合,在步骤参数处单击打开编辑器,进入位姿调整工具。然后单击右下角的下一步,检查过滤感兴趣区域外的位姿步骤是否有位姿输出(单击
按钮,查看左侧可视化区是否输出了麻袋位姿),如输出结果无误,再检查角度过滤步骤是否有位姿输出。如果麻袋存在明显倾斜,但位姿正确,可适当调大最大角度差。
问题四:路径规划失败,末端工具与场景物体碰撞
问题现象
运行Mech-Viz工程时,弹窗提示“路径规划失败,末端工具与场景物体碰撞”。
以下图为例,由于夹具正前方存在凸出的真空管,且垛位离围栏较近,机器人抓取靠近围栏处的麻袋时,容易检测到夹具凸出部分将与围栏碰撞,导致麻袋不可抓取。
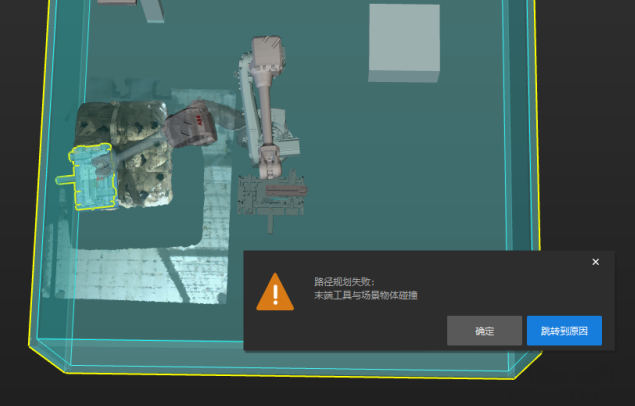
解决方法
-
如果夹具在 TCP 的 Y 轴方向较为突出,需将靠近场景围栏的麻袋位姿的 Y 轴调整至指向垛心的方向,方法如下。
选中调整位姿步骤组合,在步骤参数中单击打开编辑器,打开位姿调整工具。在默认的预设模式下,设置方向调整方式为指向/指离垛心(拆垛),设置应用场景为指向,然后设置需要旋转的轴为 Y 轴,并通过拖拽器设置垛心,即可使麻袋位姿的 Y 轴指向至垛心方向。
-
如果夹具在 TCP 的 X 轴方向较为突出,需将靠近场景围栏处的麻袋位姿 X 轴调整至指向垛心的方向,方法如下。
选中调整位姿步骤组合,在步骤参数中单击打开编辑器,打开位姿调整工具。在默认的预设模式下,设置方向调整方式为指向/指离垛心(拆垛),设置应用场景为指向,然后设置需要旋转的轴为 X 轴,并通过拖拽器设置垛心,即可使麻袋位姿的 X 轴指向至垛心方向。
上述操作完成后,即可使麻袋位姿的 X 轴或 Y 轴指向垛心的方向。

问题七:路径规划失败,路径点不可达
问题现象
使用Mech-Viz进行路径规划时,路径规划失败,弹窗提示“路径点不可达”。
例如,使用四轴机器人进行麻袋拆垛时,路径规划失败,路径点不可达。但可手动控制机器人到达整个垛型的任意位置,且Mech-Vision工程可输出视觉结果。

可能原因
一般情况下,麻袋来料不平整,识别到的麻袋位姿 Z 轴可能与机器人基坐标系 Z 轴存在 X、Y 方向上的夹角。
四轴机器人只有 X、Y、Z和绕 Z 轴旋转四个自由度,在麻袋位姿 Z 轴与机器人基坐标系下 Z 轴夹角较小时,Mech-Viz会自动矫正物体位姿的 Z 轴,以满足抓取规划。但夹角较大时将直接告警,导致无法抓取。
解决方法
在Mech-Vision工程输出视觉结果之前,对麻袋位姿 Z 轴进行矫正。矫正麻袋位姿 Z 轴前需先判断位姿 Z 轴与机器人基坐标系 Z 轴夹角是否在合理范围内,避免误矫正了确实倾斜超限需要正常报警的麻袋。具体矫正方法如下。
-
在调整位姿步骤组合后添加两个使位姿的轴旋转至指定方向(带对称性约束)步骤。
-
将第一个使位姿的轴旋转至指定方向(带对称性约束)步骤中需要旋转的轴设置为Z轴、需要固定的轴设置为X轴。
-
将第二个使位姿的轴旋转至指定方向(带对称性约束)步骤中需要旋转的轴设置为Z轴、需要固定的轴设置为Y轴。

经过以上参数设置,即可在 X 轴、Y 轴两个旋转方向上矫正位姿 Z 轴,使 Z 轴竖直朝上。