Notice¶
Attention
Only relying on point cloud collision detection to avoid collisions with fixed objects is not reliable enough. For fixed objects, their models should be added directly to the scene and more collision constraints should be used.
This is because the set threshold of the number of collision points with the point cloud, the threshold of the collision area and volume with the point cloud are generally used to tolerate errors, such as spatial noise, recognition deviation, small deviations of jig model, etc. And if the recognized point cloud is sparse and noisy, or a large number of point clouds are missing due to reflection, the effect of point cloud collision detection may be bad.
For example, in the following cases, it is not feasible to rely solely on point cloud collision detection:
Take the application of the crankshaft as an example, the threshold is 100 points, and these 100 points are usually used to tolerate the point cloud error of the crankshaft. If the crankshaft at the border of the feed box does not collide with the gripper jaws, and the gripper and the feed box coincide 98 points, under this situation, because the feed box does not have a scene model added, the software cannot calculate the collision and the number of point cloud collisions is smaller than the threshold. The softerware will ignore that there is collision and plan to grab, causing the jaws to collide with the feedbox.
In most scenarios, the point cloud is just a shell on the top surface. In case of the situation shown in the figure below, it is impossible to detect the collision between the jig and the feed box, because there is no point cloud in the feed box where the jig is located.
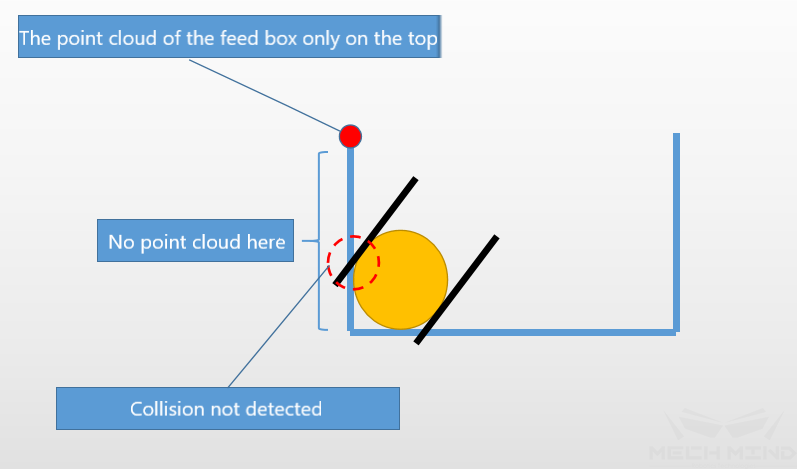