Pallet¶
Palletizing related modules are divided into five according to different application requirements. Users can choose one of them to connect according to the requirements.
smart_pallet_pattern - Choose common pallet patterns for palletizing
general_visual_pallet - Finish palletizing based on visual recognition results
mixed pallet - Palletizing objects with different sizes
custom_pallet_pattern - User-defined stacking rules
optimal_pallet - Plan the optimal pallet pattern according to the pallet and box size
Parameters¶
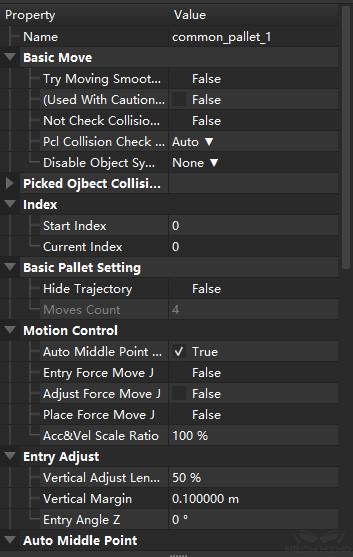
- Index
The meaning of this parameter is to index the box to be placed, counting starts from 0. The application method is: when starting the code from an empty stack, this value starts from 1. If four boxes have already been stacked, the stacking process is suspended for some reasons at this time. When the stacking is started again, it is not necessary to manually remove the boxes that have been stacked on the pallet and start again from the beginning. Instead, you only need to set the start index to 4. The program can automatically continue to execute the palletizing process from the fifth box.
- BasicPalletSetting
hideTrajectory
movesCount
- MotionControl
autoMiddlePointForceMoveJ
entryForceMoveJ
adjustForceMoveJ
placeForceMoveJ
accVelScaleRatio: As shown in the figure below, when approaching the stack, it is divided into three stage. The first stage approaching the stack is in purple, and the other two stage are the paths for actually placing the boxes. According to the field application, sometimes the robot is required to move faster when approaching the stack, and slower when actually placing the boxes, in such a case, the speed/acceleration of the two stages of approaching the stack (purple) and actually placing the boxes can be restricted by this parameter. The speed and acceleration approaching the stack (purple) are the values specified in Basic Move General Parameters, referred to as v1, and the speed/acceleration of the next two stages of robot motion are v1 \(\times\) this parameter.
- EntryAdjust
There are three parameters in this set, which control the entry path of boxes together when they are stacked. The purpose is to avoid the collision of the stacked boxes due to accuracy or other reasons when the robot directly lowers the boxes vertically. Adjust the entry path so that the box approaches the stacked box at a certain angle and then lowers it vertically;
For each box, there are 4 positions in the stack. The three parameters in this set control the three parameters, as shown by the red dots in the figure below, which are entry, adjust and place. The perspective below is the front view of the box.
verticalAdjustLenRatio: This parameter is the height ratio when approaching the stacked box, which is equal to (verticalAdjustLen / box height). The value range is 0 – 1, with no unit. The default value is 0.5.
verticalMargin: This parameter is the height margin of the cut-in point. The value ranges from 0 to infinity, and the unit is millimeter. Generally, it is set to a number greater than 0 to leave a margin. The specific value depends on the application scene.
entryAngleZ: This parameter is α in the above figure. It is the angle between the path entry-adjust and the vertical direction. The unit is °, and the value range is -80 – 80 °. The recommended default value is 30 ° – 45 °.
- autoMiddlePoint:
The pink ball as shown in the figure below, this set of parameters controls the fourth position in the stack is mentioned above-the position of the middle point.
X/Y: Set the position x, y of the pink ball in the base coordinate system of the robot. The software will automatically calculate reasonable midpoint coordinates for stacks of different heights based on this position.
minZ: The minimum absolute z-height when approaching (purple path). (And the maximum height of this floor). As shown below
isMiddlePointTrajVertical
extendedDist
Attention
The autoMiddlePoint is only an indication of the direction when approaching the stack, not the point that the robot actually arrives. Therefore, the pink ball shall be as far away from the pallet as possible. If the ball is too close to the stack, during the process of placing the box, it may cause crushing collision.
- AdjustPalletViaVision
This parameter can dynamically adjust the position of the stack by the vision service
needAdjustPalletPose: The default is False. When the position of the stack is required to be adjusted dynamically, select it as true. When the program proceeds to this task, it will call the vision service to identify the location of the stack.
visionToAdjustPallet: Fill in the name of the vision project to identify the location of the stack. When the program proceeds to this task, it will call the vision service according to the vision project name.
BasicMove¶
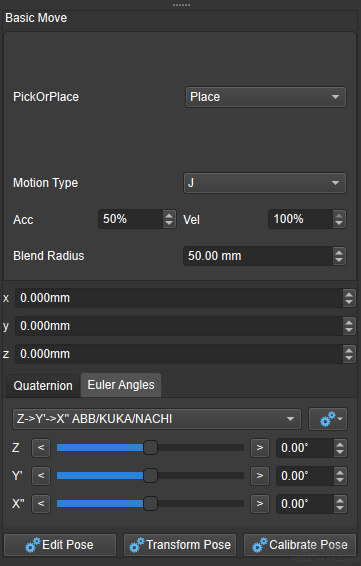
Here you can set the position of pallet and move parameters, etc. The function is the same as other Basic Move General Parameters , so it won’t be described here.