Plan History¶
This section introduces the function of Plan History.
The following topics are covered:
Overview¶
The overall plan history is laid out in a tree structure, which contains every node in the whole process of path planning. Comparing to the log, plan history contains more details of every node (especially when there is an error) in the process.
Some errors are serial errors, which means that if the error occurs at one of the nodes, the final plan result will fail. For example, a certain joint position is set wrong, and the robot cannot move to the planned waypoint.
Some errors are parallel errors, which means that the final plan result will still succeed if the planning at one of the parallel nodes is successful. For example, when Mech-Viz attempts to pick with the pick points sent by Mech-Vision, if either one of the pick points works, the workobject can be picked successfully.
Hint
You can focus on the nodes where errors occur when running the project.
Visualize Collision¶
Compute and Record Collision Contacts¶
Computing and recording collisions are usually used for collision result visualization.
In Computation Settings in the Collisions panel, select Compute complete collision contacts of each candidate solution and Save in plan history options, all collisions will be recorded and saved in the plan history.
Visualize Collisions with Plan History¶
Click Display and check the box before Show Collision While Planning.
Collision with the scene object
Click the Step in which the collision occurs, and the object that collides with the robot in the scene will be highlighted.
Click the object that collides with the robot, and the object will be highlighted.
Collision with the point cloud
Click the Step in which the collision occurs, and the object that collides with the robot in the scene will be highlighted.
Click the collision volume, and the point cloud that collides with the robot will be highlighted.
When the point cloud collides with the robot, if the collision is not recorded, only the other collided object will be highlighted.
Collision with the workobject
When the workobject collides with the robot, the workobject will be highlighted.
Causes of Common Failures and Fixes¶
Self Collision¶

Cause: Forearm and robot base collided.
Fix: Adjust the pose to avoid the self collision.
Collide with Scene Object¶

Cause: End tool and scene object [1] collided.
Fix: Check the pose of the collided scene object. if the pose of the scene object cannot be changed, you can adjust the pose in the current Step.
Waypoint Unreachable¶

Cause: The waypoint is out of the reachable range of the robot. The robot cannot reach the waypoint.
Fix: Adjust the pose to make the robot reach the waypoint.
Cross the Collision Volume Threshold¶
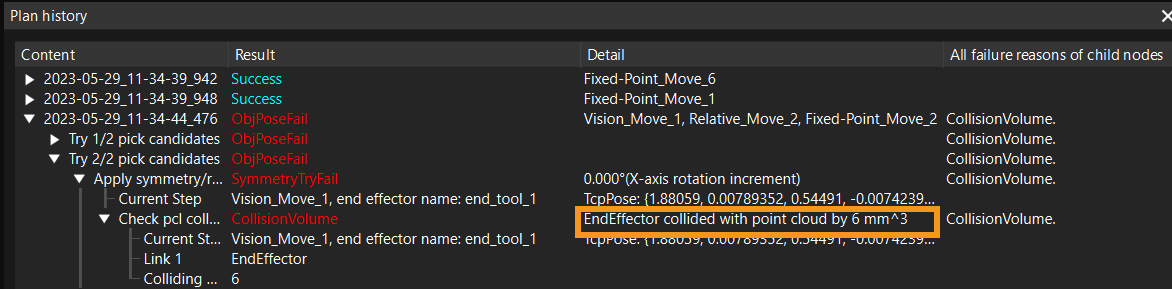
Cause: The collision volume of the end tool and the point cloud is greater than the threshold.
Fix: Adjust the collision volume threshold according to the detected collision volume and the actual tolerance of collision. Or adjust the TCP, pick points, and pose of the collision model of the end tool according to the actual situation.