Learning Guidance for 3D Robot Guidance
Learning guidance
|
Overview of 3D Robot Guidance
The 3D robot guidance solution integrates Mech-Mind’s sensing, perception, robot programming/planning technologies into a comprehensive solution, aiming to address the challenges that robots face in complex, unknown, or dynamic environments.
|
For the software and corresponding versions required for deploying this solution, please refer to Recommended Software Version Combinations for 3D Robot Guidance Solution.
Getting Started
Provides getting started tutorials for new users and beginners. By learning these tutorials, you can have a brief look at the Mech-Mind’s 3D robot guidance solution and attempt to build your first 3D vision–guided robotic application.
Tutorial: Vision Guided Robotic Picking of Metal Parts
|
|
Tutorial: Vision Guided Robotic Depalletizing of Cartons
|
Practical Application Deployment
Provides the approach to, operation guide of, and experience for deploying applications in actual projects. After you learn about the 3D robot guidance solution, you can continue to learn the knowledge and expertise required for deploying 3D vision–guided robotic applications in this part.
The approach to deploying a 3D vision–guided robotic application is shown in the following figure.


Vision solution design refers to selecting the hardware models, and determining mounting modes and vision processing methods according to project requirements.

For details, refer to Vision Solution Design.

Vision system hardware setup refers to integrating the hardware (camera and industrial PC) into the actual environment to support the normal operation of the vision system.

The process of vision system hardware setup may vary depending on the camera mounting modes. For details, refer to Vision System Hardware Setup.

Vision system hardware setup completes the hardware integration of the vision system with the robotic system, while robot communication configuration will complete the communication integration between the two systems. This ensures that the vision system and the robot side can exchange data accurately in real time.
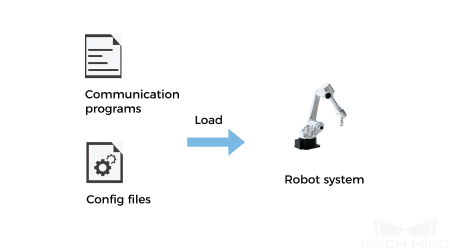
To configure the robot communication, you usually need to load the communication program and configuration files provided by Mech-Mind into the robotic system and complete corresponding communication configurations. For details, refer to Robot Communication Configuration.

The robot’s perception of the environment needs to be realized through the "eyes (camera)". Hand-eye calibration is used to establish the transformation relationship between the camera reference frame and the robot reference frame.

For different robot types, camera mounting modes, and communication modes, the calibration tool of the Mech-Mind Mech-Vision software has provided standardized calibration procedures, helping you complete hand-eye calibration easily. For details, refer to Hand-Eye Calibration.

Vision project configuration is crucial to the deployment of a 3D vision–guided robotic application. It enables recognition and localization of target objects.

For details, refer to Vision Project Configuration.

The ultimate goal of deploying a 3D vision–guided robotic application is to achieve successful picking. In this phase, you need to build a robot picking workflow so that the robot can pick objects accurately under the guidance of vision results.

The ways to build the robot picking workflow may vary depending on the communication modes selected. For details, refer to Picking.
For practical guidance for more application scenarios, please refer to Typical Case Practices of 3D Robot Guidance.
Troubleshooting and Maintenance
You can refer to this part for troubleshooting guidance or help if a fault or anomaly occurs during the application deployment or subsequent production.
Provides commissioning engineers with the commissioning experience and ways to find help during application deployment.
Commissioning experience: Community - Knowledge Base category
Find help: Community - Q&A category
Provides field engineers with common issues and corresponding solutions during production.
Troubleshooting: Service Manual | Community - Troubleshooting category
Find help: Community - Q&A category