Modbus TCP - MELSEC-Q Series PLC Commands¶
This topic introduces the commands for the communication between a Mitsubishi MELSEC-Q Series PLC and Mech-Mind Software Suite through the Mech-Center Modbus TCP Standard Interface.
Introduction¶
Mech-Center Modbus TCP Standard Interface¶
Mech-Center supports communication based on the Modbus TCP protocol. With the Standard Interface option Modbus TCP SLAVE selected, Mech-Center serves as the slave and communicates with the master device.
Please refer to Register Map for detailed register map table for Modbus TCP in Mech-Center.
PLC Example Programs¶
MODBUS_TCP_Protocol Configuration.tpc (for setting up Modbus TCP communication)
MODBUS TCP_Q_Simple_Label.GXW (for realizing the functions of interface commands)
Note
File location: XXXX/Mech-Center-xxx/Robot_Interface/Modbus TCP/MITSUBISHI Q serial (the installation directory of Mech-Center)
Please copy the files to the computer with GX Works2 installed.
Commands¶
Start Mech-Vision Project¶
This command is for applications that use Mech-Vision but not Mech-Viz. It runs the corresponding Mech-Vision project to acquire and process data, as well as sending the image capturing pose for Eye-In-Hand installation.
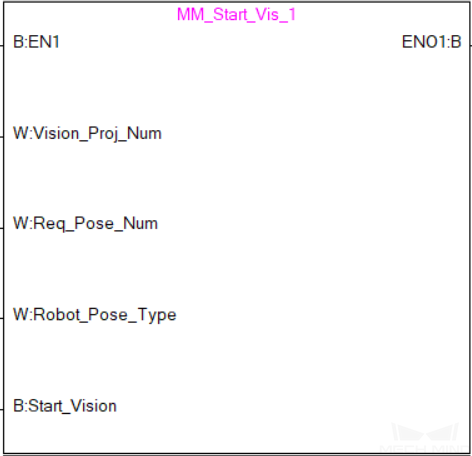
Parameters
Input parameters
Vision_Proj_Num
Mech-Vision Project ID, from 1 to 99.
Can check and adjust in
Req_Pose_Num
Number of vision points for Mech-Vision to send, from 0 to 20, where 0 means “send all”.
Robot_Pose_Type
Set the image-capturing pose for the robot to send, from 0 to 2.
0: Do not send image-capturing pose (for Eye To Hand) 1: Send image-capturing pose as joint positions 2: Send image-capturing pose as robot flange pose
Label Camera_User.Robot_Pose
The image-capturing pose sent by the robot, as FLOAT (Single Precision)(0..5).
Start_Vision
Start the Mech-Vision project at the rising edge.
Returned data from the MM_Camera global label
Status_Code
1102 is returned if no error occurred.
For other values, please refer to Status Codes and Trouble Shooting for the corresponding error.
Example
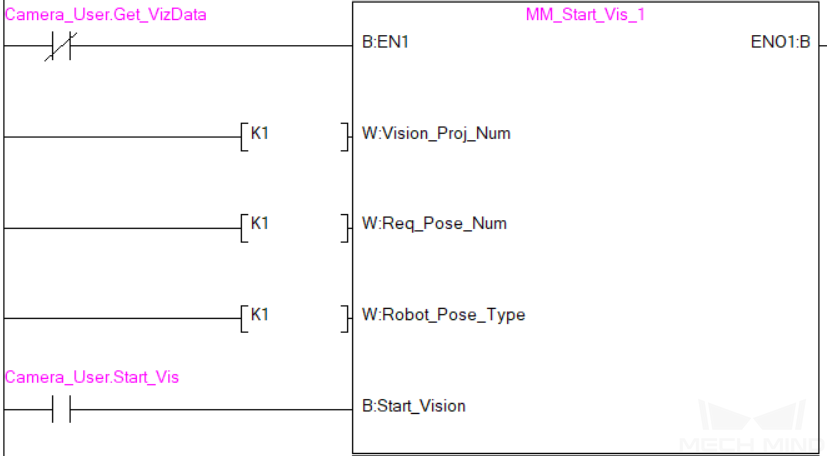
When Camera_User.Start_Vis is at the rising edge, this example runs Mech-Vision project No. 1, asks the project to send over 1 vision point, and sends the robot joint positions when the Mech-Vision project is started as the image-capturing pose to Mech-Center.
Get Vision Target(s)¶
This command is for applications that use Mech-Vision but not Mech-Viz. It obtains the vision result from the corresponding Mech-Vision project.
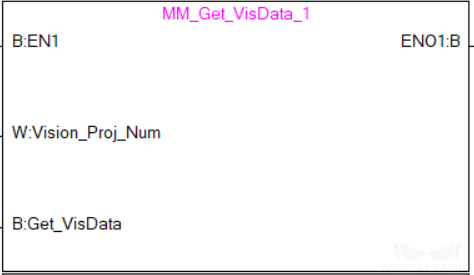
Parameters
Input parameters
Vision_Proj_Num
Mech-Vision Project ID, from 1 to 99.
Can check and adjust in
.Get_VisData
Obtain the vision result from the Mech-Vision project at the rising edge.
Returned data MM_Camera global label
Status_Code
1100 is returned if no error occurred.
For other values, please refer to Status Codes and Trouble Shooting for the corresponding error.
Status_of_Pose_Sent
1 represents that the target data written in are new.
After the PLC reads the pose data, please run the MM_Empty_Target FB to reset the register to 0.
Number_of_Pose_Sent
Store the number of received vision points, from 1 to 20.
Target_Pose
Store the received target poses as TCPs.
Target_Label
Store the integer labels corresponding to the poses. Labels are set in Mech-Vision.
Example
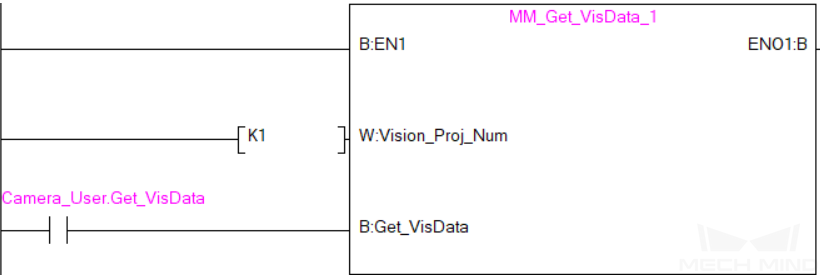
When Camera_User.Get_VisData is at the rising edge, this example obtains the vision result from Mech-Vision project No. 1.
Switch Mech-Vision Recipe¶
This command specifies which parameter recipe of the Mech-Vision project to use. For more information on parameter recipe, please see Parameter Recipe.
Note
This command must be executed BEFORE MM_Start_Vis.
The corresponding Mech-Vision project must have parameter recipes already configured and saved.
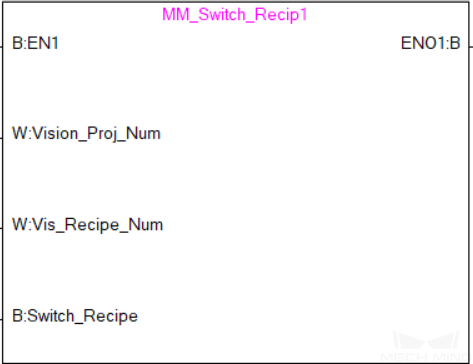
Parameters
Input parameters
Vision_Proj_Num
Mech-Vision Project ID, from 1 to 99.
Can check and adjust in
.Vision_Recipe_Num
The number of a parameter recipe in the Mech-Vision project, from 1 to 99.
Switch_Recipe
Switch the parameter recipe at the rising edge.
Returned data from the MM_Camera global label
Status_Code
1107 is returned if no error occurred.
For other values, please refer to Status Codes and Trouble Shooting for the corresponding error.
Example
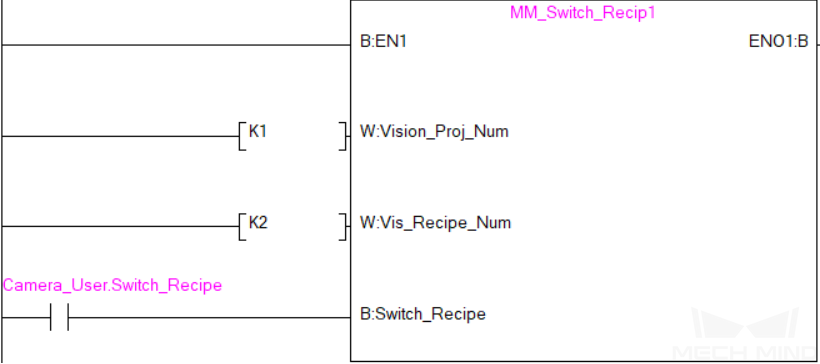
When Camera_User.Switch_Recipe is at the rising edge, this example switches the parameter recipe used to No. 2 in Mech-Vision project No. 1.
Start Mech-Viz Project¶
This command is for applications that use both Mech-Vision and Mech-Viz. It runs the corresponding Mech-Viz project (which triggers the corresponding Mech-Vision project to run), and sets the initial joint positions of the simulated robot in Mech-Viz.
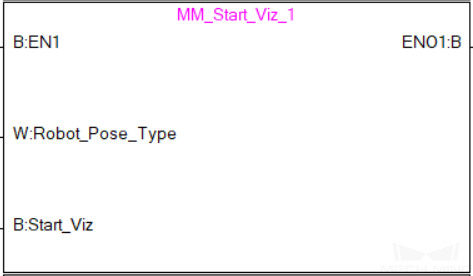
Parameters
Input parameters
Robot_Pose_Type
The initial joint positions for the simulated robot in Mech-Viz, 0 or 1.
0: Set the initial joint positions of the simulated robot to [0,0,0,0,0,0] 1: Set the initial joint positions of the simulated robot to the current joint positions of the real robot
Label Camera_User.Robot_Pose
The current joint poisions of the robot, as FLOAT(Single Precision)(0..5).
Start_Viz
Start the Mech-Viz project at the rising edge.
Note
When the scene contains object models that obstruct the robot to move from [0,0,0,0,0,0] to the first target, the value of Robot_Pose_Type must be set to 1.
Returned data from the MM_Camera global label
Status_Code
2103 is returned if no error occurred.
For other values, please refer to Status Codes and Trouble Shooting for the corresponding error.
Example
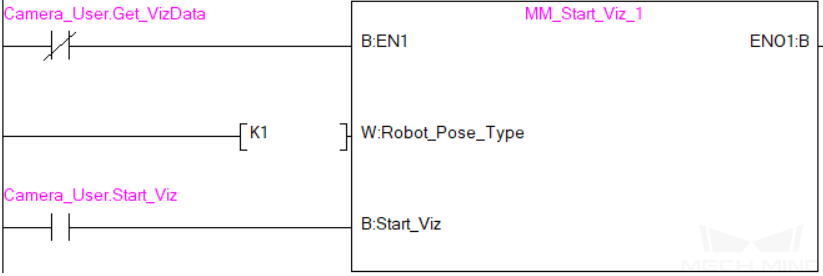
When Camera_User.Start_Viz is at the rising edge, this example runs the corresponding Mech-Viz project, and sets the initial joint positions of the simulated robot to the current joint positions of the real robot.
Stop Mech-Viz Project¶
This command stops the execution of the Mech-Viz Project. This command is only needed if the Mech-Viz project falls into an infinite loop or cannot be stopped normally.
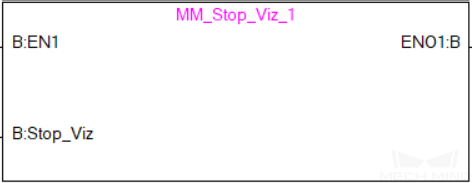
Parameters
Input parameters
Stop_Viz
Stop the execution of the Mech-Viz project at the rising edge.
Returned data from the MM_Camera global label
Status_Code
2104 is returned if no error occurred.
For other values, please refer to Status Codes and Trouble Shooting for the corresponding error.
Example
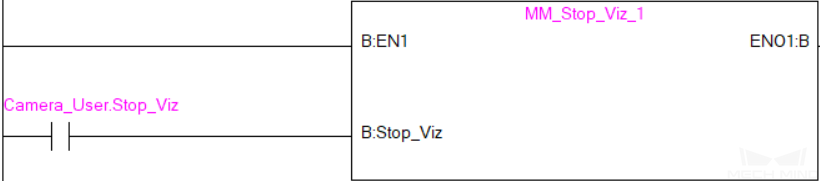
When Camera_User.Stop_Viz is at the rising edge, this example stops the execution of the Mech-Viz project.
Select Mech-Viz Branch¶
This command is used to select along which branch the Mech-Viz project should proceed. Such branching is achieved by adding branch_by_msg Task(s) to the project. This command specifies which exit port such Task(s) should take.
Note
MM_Start_Viz must be executed BEFORE this command.
When the next Task to be executed in Mech-Viz is a branch_by_msg Task, Mech-Viz will wait for this command to send the exit port number it should take.
The name of all branch_by_msg Tasks in the Mech-Viz project must be changed to integers between 1 and 99, and the names should be unique among all Tasks in the project.
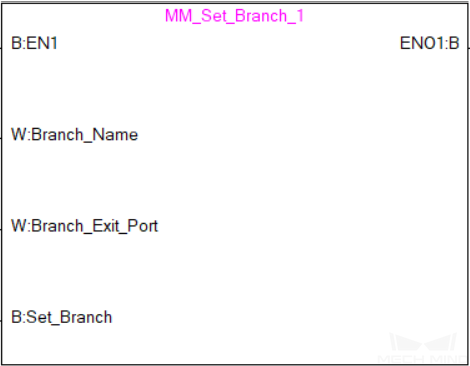
Parameters
Input parameters
Branch_Name
Name of the branch_by_msg Task, from 1 to 99.
Branch_Exit_Port
The number of the exit port to take, from 1 to 99.
Add 1 to the port number displayed in Mech-Viz. E.g., value 1 corresponds to exit port 0 in Mech-Viz.
Set_Branch
Sets the branch to take at the rising edge.
Returned data from the MM_Camera global label
Status_Code
2105 is returned if no error occurred.
For other values, please refer to Status Codes and Trouble Shooting for the corresponding error.
Example
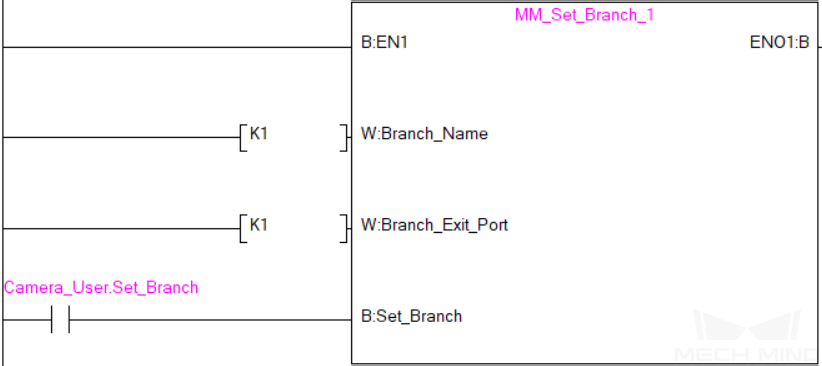
When Camera_User.Set_Branch is at the rising edge, this example tells Mech-Viz to take exit port 1 for the branch_by_msg Task named 1.
Set Move Index¶
This command sets the value for the Current Index parameter of Mech-Viz Tasks. Tasks that have this parameter include move_list, move_grid, custom_pallet_pattern, and smart_pallet_pattern.
Note
MM_Start_Viz must be executed BEFORE this command.
The name of all Tasks with index parameters in the Mech-Viz project must be changed to integers between 1 and 99, and the names should be unique among all Tasks in the project.
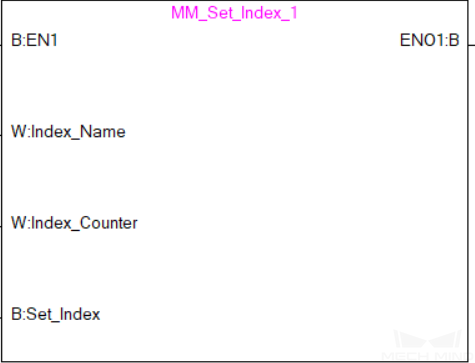
Parameters
Input parameters
Index_Name
Task ID of the Task with the index parameter. The Task ID can be read in the Task’s parameters.
Index_Counter
The index value that should be set the next time this Task is executed.
When this command is sent, the current index value in Mech-Viz will become the parameter value minus 1.
When the Mech-Viz project runs to the task specified by this command, the current index value in Mech-Viz will be increased by 1 to become the parameter’s value.
Set_Index
The trigger signal to set the index. The rising edge does the trigger.
Returned data from the MM_Camera global label
Status_Code
2106 is returned if no error occurred.
For other values, please refer to Status Codes and Trouble Shooting for the corresponding error.
Example
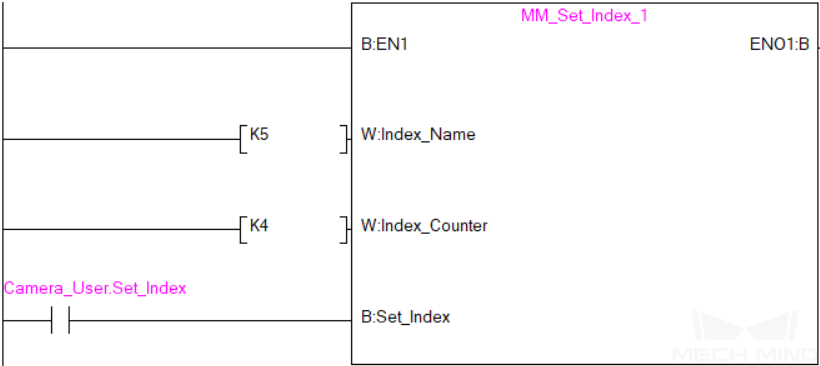
When Camera_User.Set_Index is at the rising edge, this example sets the Current Index value to 3 for the Task named 5. When the Task is executed, the Current Index value will be added 1 and become 4.
Get Planned Path¶
This command obtains the planned path from Mech-Viz.
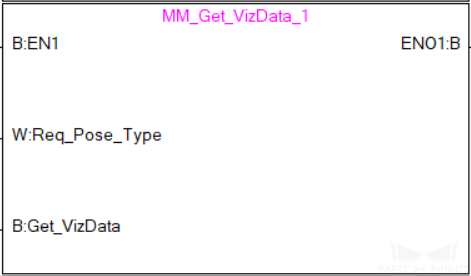
Parameters
Input parameters
Request_Pose_Type
Whether Mech-Viz should send targets as joint positions or TCPs, 1 or 2.
1: Mech-Viz sends joint positions 2: Mech-Viz sends TCPs
Get_VizData
Obtains the planned path from Mech-Viz at the rising edge.
Attention
The Request_Pose_Type here and the Robot_Pose_Type in the MM_Start_Vis and MM_Start_Viz FBs all correspond to the same Pose Type label in the MM_Camera global label. Therefore, if these parameters are set to different values, the programming should ensure that the two values do not take effect at the same time.
Returned data from the MM_Camera global label
Status_Code
2100 is returned if no error occurred.
For other values, please refer to Status Codes and Trouble Shooting for the corresponding error.
Status_of_Pose_Sent
1 represents that the target data written in are new.
After the PLC reads the pose data, please run the MM_Empty_Target FB to reset the register to 0.
Number_of_Pose_Sent
Store the number of received targets, from 1 to 20.
Index_of_Vision_Picking_Point
Store the position of the visual_move target in the path.
Example path: move-1, move-2, visual_move-3, move-3 In this path, the position of the visual_move target is 3. If the path does not contain visual_move target, the return value is 0.
Target_Pose
Store the received target poses.
Target_Label
Store the integer labels corresponding to the poses. Labels are set in Mech-Vision.
Speed_Percentage
Store the velocity settings corresponding to the poses.
Example
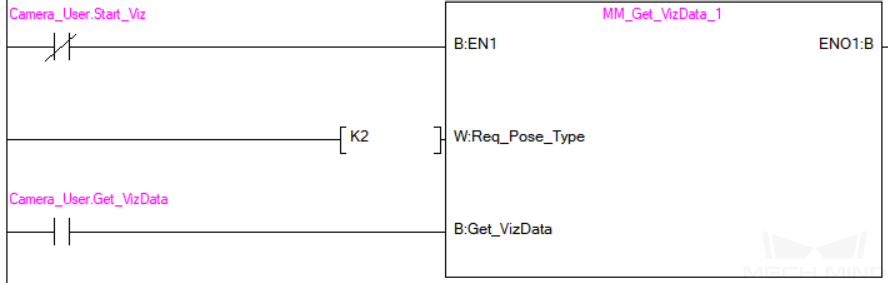
When Camera_User.Get_VizData is at the rising edge, this example obtains the planned path from Mech-Viz in the form of TCPs.
Get DO List¶
This command obtains the planned DO signal list for controlling multiple sections of a sectioned vacuum gripper.
Note
MM_Get_VizData must be executed BEFORE this command.
Please configure the Mech-Viz project based on the template project in XXXX/Mech-Center-xxx/tool/viz_project/suction_zone, and set the suction cup configuration file in the Mech-Viz project.
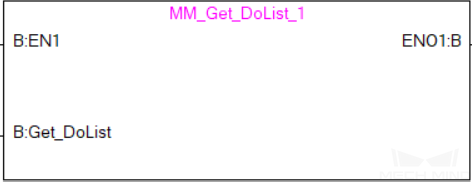
Parameters
Input parameters
Get_DoList
Obtains the planned DO signal list from Mech-Viz at the rising edge.
Returned data from the MM_Camera global label
Status_Code
2102 is returned if no error occurred.
For other values, please refer to Status Codes and Trouble Shooting for the corresponding error.
DO_LIST
The list of 64 DO values, in the range of 0 to 999, with -1 being the placeholder value.
Example
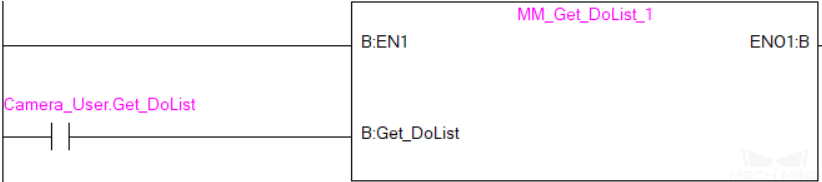
When Camera_User.Get_DoList is at the rising edge, this example obtains the planned DO signal list from Mech-Viz and stores it in the DO_LIST label.
Input Object Dimensions to Mech-Vision¶
This command inputs object dimensions to the Mech-Vision project.
Note
This command must be executed BEFORE MM_Start_Vis.
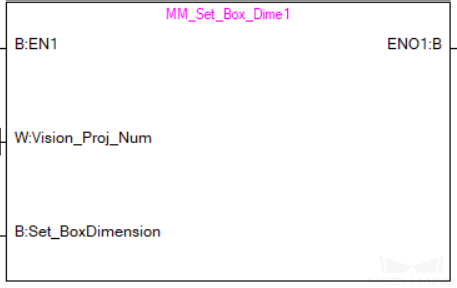
Parameters
Input parameters
Vision_Proj_Num
Mech-Vision Project ID, from 1 to 99.
Can check and adjust in
.Label Camera_User.External_Input_Box_Dimention
The 3D dimensions (in mm) to be input to the Mech-Vision project, as an array of 3 real numbers.
Set_Box_Dimention
Input the object dimensions to the Read Object Dimensions Step in the Mech-Vision project at the rising edge.
Returned data from the MM_Camera global label
Status_Code
1108 is returned if no error occurred.
For other values, please refer to Status Codes and Trouble Shooting for the corresponding error.
Example
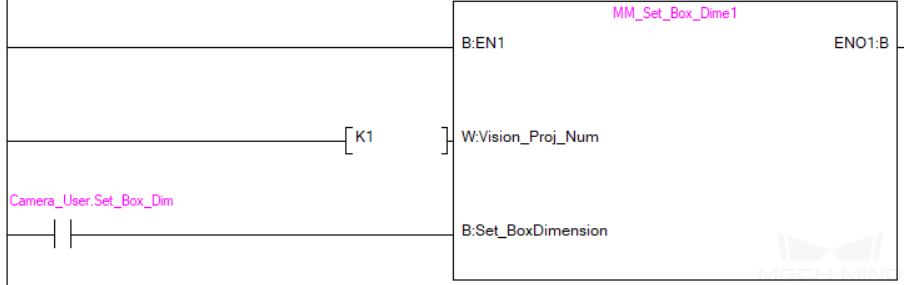
When Camera_User.Set_Box_Dimention is at the rising edge, this example sets the object dimensions in the Read Object Dimensions Step in the Mech-Vision project No. 1 to the values in External_Input_Box_Dimention.
Input TCP to Mech-Viz¶
This command inputs TCP data to the outer_move Task.
Note
This command must be executed BEFORE MM_Start_Viz.
Please configure the Mech-Viz project based on the template project in XXXX\Mech-Center-xxx\tool\viz_project\outer_move, and put the outer_move Task at a proper position in the workflow.
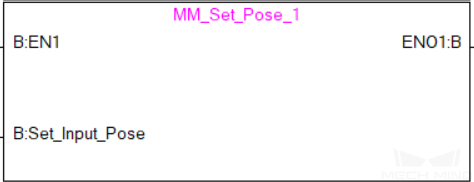
Parameters
Input parameters
Label Camera_User.External_Input_Pose
The TCP data to be input to Mech-Viz (in mm), as an array of 6 real numbers.
Set_Input_Pose
Input the TCP data to the outer_move Task in the Mech-Viz project at the rising edge.
Returned data from the MM_Camera global label
Status_Code
2107 is returned if no error occurred.
For other values, please refer to Status Codes and Trouble Shooting for the corresponding error.
Example
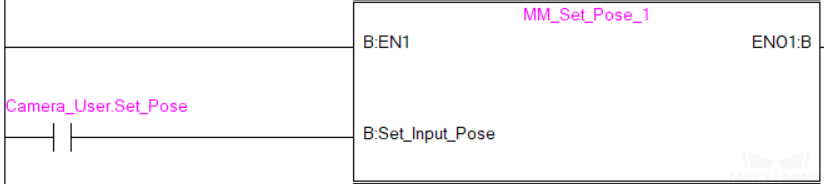
When Camera_User.Set_Pose is at the rising edge, this example sends the TCP data stored in External_Input_Pose to the outer_move Task in the Mech-Viz project.
Get Software Status¶
This command is currently capable of checking whether Mech-Vision is ready to run projects. In the future, this command can be used for obtaining the execution status of Mech-Vision, Mech-Viz and Mech-Center.
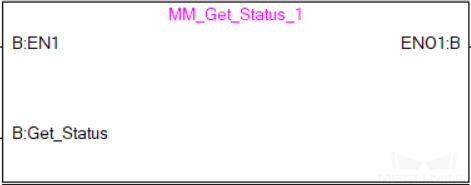
Parameters
Input parameters
Get_Status
Check whether Mech-Vision is ready to run projects at the rising edge.
Returned data from the MM_Camera global label
Status code
Software status. 1101 means the Mech-Vision project is ready to run. Other codes mean the project is not ready.
Example
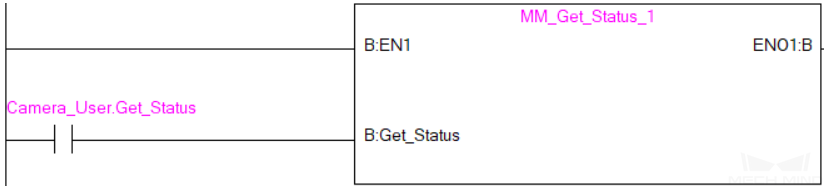
When Camera_User.Get_Status is at the rising edge, this example checks the status code and stores it in the Status_Code label.
Clear Target Data¶
This command clears the obtained data stored in the Target_Pose, Target_Label and Speed_Percentage.
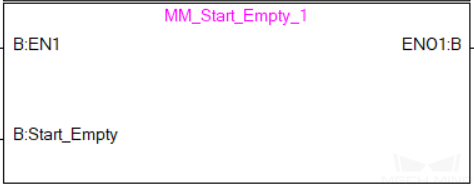
Parameters
Input parameters
Start_Empty
Clear the data stored in Target_Pose, Target_Label and Speed_Percentage when value set to 1.
Returned data from the MM_Camera global label
Status_Code
3103 is returned if no error occurred.
For other values, please refer to Status Codes and Trouble Shooting for the corresponding error.
Target_Pose
Obtained target poses.
Target_Label
Obtained labels.
Speed_Percentage
Obtained velocity settings.
Example
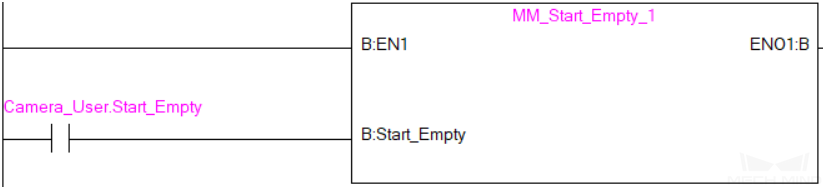
When the value of Camera_User.Start_Empty is set to 1, the data stored in the Target_Pose, Target_Label and Speed_Percentage are cleared.
Description of the Status Codes¶
Please refer to Status Codes and Trouble Shooting for detailed information.